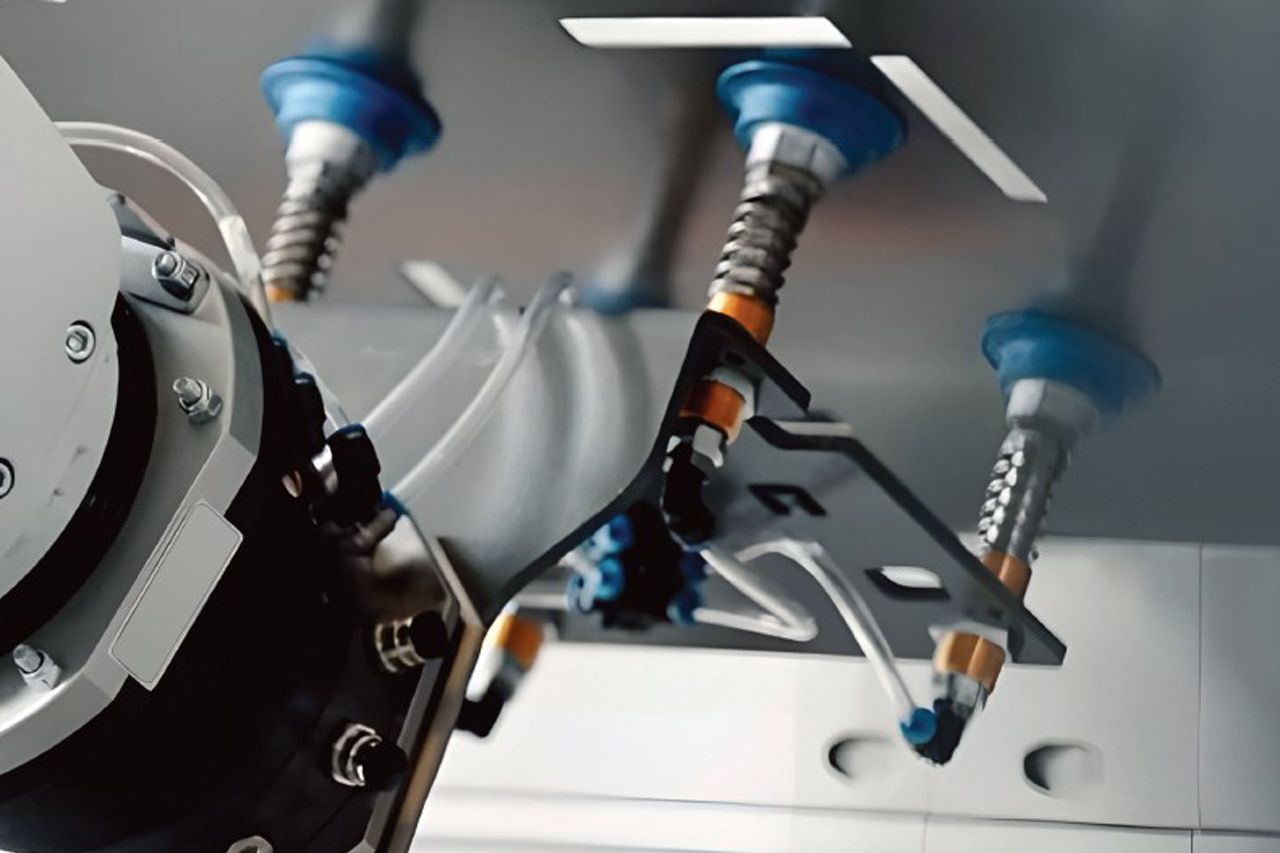
Blog Maximizing Efficiency and Capacity with Press Brake Automation
Press brake automation stands at the forefront of this transformation, offering manufacturers the ability to significantly enhance production capacity, improve precision, and overcome challenges such as labor shortages and operator fatigue. As the demand for faster, more efficient bending processes grows, automation technologies, including offline programming and robot-tended systems, have become invaluable tools for optimizing press brake operations
Overcoming Labor Shortages and Enhancing Productivity
One of the most pressing issues facing manufacturers today is the shortage of skilled operators. As businesses strive to meet customer demands, the ability to run operations efficiently without over-relying on human labor becomes increasingly critical. Press brake automation offers a solution by reducing the number of operators required to run machines, thereby minimizing the impact of labor shortages.
Modern offline programming systems allow for the creation of ready-to-run programs, eliminating the need for operators to spend valuable time programming machines at the production floor. With automated press brake systems, a single operator can manage multiple machines, enhancing overall flexibility and productivity. Moreover, these systems can run during off-shifts or weekends, ensuring continuous operation and maximizing throughput without the need for additional labor.
Streamlining Setup and Tooling Changeovers
A significant advantage of automated press brake systems is their ability to streamline the setup process. Traditional manual setups are time-consuming and prone to errors, often leading to production delays and increased costs. Automated systems, however, drastically reduce setup times by using automated tooling changeovers and efficient offline programming, which can generate and verify robot programs before they even reach the production floor.
These systems store and retrieve bending programs quickly, reducing the time spent on manual adjustments and improving consistency across shifts. This reduction in setup time is particularly beneficial for handling high-mix, low-volume operations where fast changeovers are crucial to maintaining production flow. With hydraulic tool clamping and quick-change segmented tools, manufacturers can further accelerate tool changes, minimizing downtime and enhancing overall machine utilization.
Enhancing Throughput with Off-Shift Automation
One of the most impactful benefits of press brake automation is its ability to operate efficiently during off-hours. Running automated systems overnight or during weekends allows manufacturers to significantly expand their production capacity without the need for additional labor. This off-shift productivity is especially valuable for meeting rising production demands without expanding shifts or increasing costs.
By leveraging automation, manufacturers can increase throughput during periods when human operators are not available, ensuring that machines are running at full capacity around the clock. This not only boosts production output but also lowers costs per part by maximizing the efficiency of every operation. With automation handling the bulk of the work during non-peak hours, operators can focus on higher-level tasks such as managing material flow, programming, and overseeing multiple bending cells.
Meeting the Demands of High-Speed Fiber Lasers
The integration of high-speed fiber laser cutting systems has revolutionized the manufacturing process, dramatically increasing cutting speeds and throughput. However, this leap in efficiency has also highlighted a critical need: matching the laser's speed with enhanced bending throughput. Press brake automation addresses this challenge by offering a solution that operates at speeds of up to one inch per second, ensuring that bending processes keep pace with the faster cutting systems.
Automated press brake systems are designed to match these high-speed requirements, ensuring that manufacturers can maintain peak productivity levels without compromising quality. With automation in place, manufacturers can eliminate the risks associated with operator fatigue and ensure consistent, high-quality results even during long production runs.
Flexibility with Mobile Press Brake Automation
While fixed press brake automation systems excel in high-volume, low-mix environments, mobile press brake automation offers the flexibility to alternate between manual and automated operations. This is particularly beneficial in environments where small-batch or complex parts are common. Mobile systems can handle high-mix operations during manual shifts and switch to fully automated production during off-hours, maximizing machine usage and improving overall efficiency.
Recent innovations in robot cell programming have significantly reduced setup times, allowing mobile systems to be programmed in as little as one minute per bend. This flexibility makes mobile press brake automation ideal for smaller, light-gauge parts, enabling manufacturers to meet the demands of both high-volume and low-volume production without compromising on quality or efficiency.
The Future of Press Brake Automation
The future of press brake automation is bright. From fixed automation systems designed for heavy-duty applications to mobile solutions offering flexibility for high-mix, low-volume environments, press brake automation is reshaping manufacturing processes across industries.
As the demand for speed, precision, and cost efficiency continues to grow, the integration of automated systems will be crucial for manufacturers looking to stay competitive. By addressing bottlenecks, optimizing tool changes, and utilizing off-shift capacity, press brake automation is paving the way for more efficient, profitable, and sustainable manufacturing operations.
In this era of technological transformation, embracing automation is no longer a luxury—it is a strategic imperative that empowers manufacturers to meet the challenges of today and tomorrow, ensuring long-term success in an increasingly competitive market.