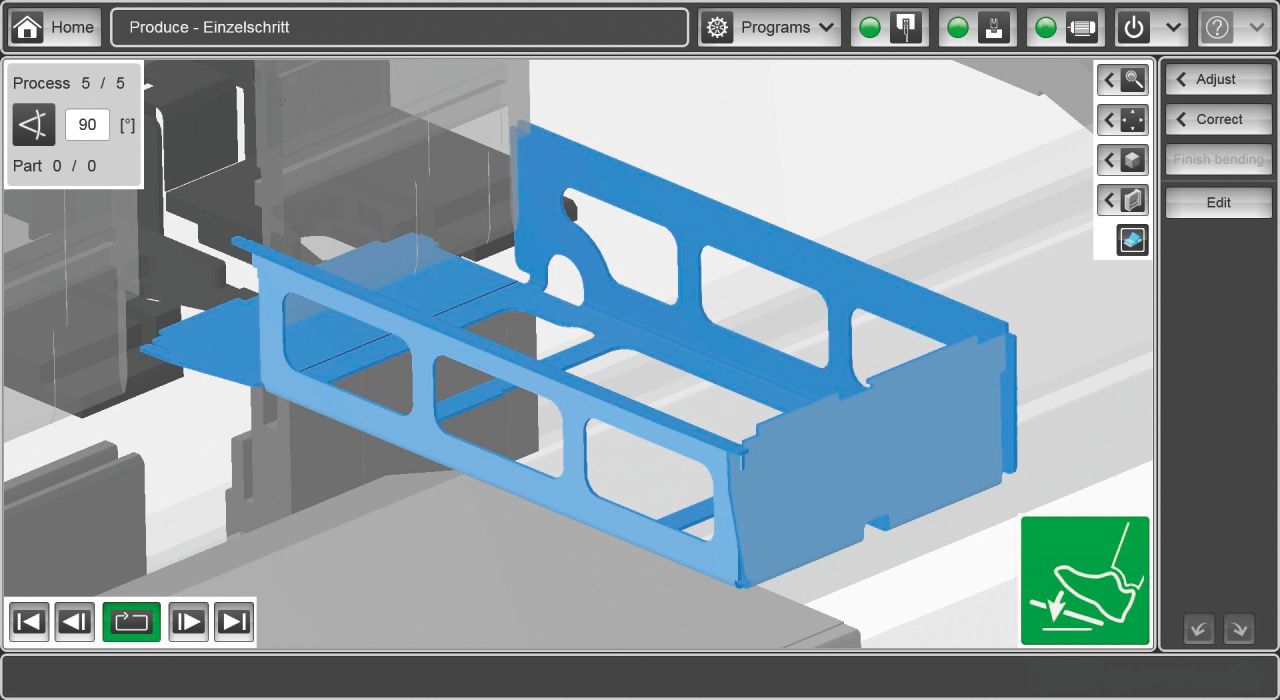
Blog Benefits of Modern CNC Press Brakes
Older press brakes were not as sophisticated and required a higher level of skill and experience to operate effectively. However, with the advent of modern CNC press brake technologies, the landscape has changed dramatically, and the experience and skill set required to operate these machines has evolved accordingly.
Easier Setups
One of the major differences between older CNC press brakes and modern CNC press brakes is the set-up process. In the past, the set-up process required a significant amount of experience and was often performed by a dedicated supervisor. However, with the advent of offline programming, the machine can now be programmed without requiring the operator to be trained in part programming. This has freed up the machine control to focus on production, allowing for increased efficiency and a higher output of parts produced per day. With the use of hydraulic clamping systems for quick change tooling, changeover times are very fast, as it takes only the press of a button to release and also to secure the tooling to the press brake ram and table clamping systems. With manual clamping systems, the changeover takes longer as each individual punch and die must be released and then re-secured manually by the operator.
One of the most visible bottlenecks with older press brakes is the limited capacity of available bending time due to the increased time necessary for their set-up. Less available bending time means fewer parts produced and less capacity for taking on additional work. This bottleneck will be most apparent when you notice a large number of parts that are waiting to be produced at the press brake. The solution could be to just add another brake, but what about finding another qualified operator? What is truly required is a more efficient press brake while not having to increase the number of them. Doing so will not only satisfy your current production capabilities but also satisfy the additional capacity required for future business.
Using Cutting Edge Technologies
One of the key benefits of modern CNC press brakes is the “smart technologies” that are built into the machine. These technologies impact not only the quality of the finished parts but also the level of experience required of the operator. For example, 3-D graphical simulations of the bending sequence prior to bending allow the operator to visualize the entire process, while CNC back gauge axes are displayed graphically to indicate the specific part of the back gauge that is being used for part positioning. If required, bend re-sequencing is easily achieved by dragging and dropping a bend step on the control. The bar code scanning of the laser-engraved part ID has enabled error-proof loading of the correct part program, while graphical and LED tool mapping displays clearly show the operator where each tool needs to be loaded and which type of tooling is to be used.
Automatic dynamic crowning ensures that the angles are consistent along the entire bend length, while thickness detection accounts for material thickness deviations and automatically re-calculates the new bottom dead center of the bend angle. Mechanical compensations, such as frame deflections, which can vary depending on the applied tonnage and temperature compensation for the hydraulic system, as it affects the frame over time with varying temperatures, are applied dynamically during the bending process without operator intervention. Laser angle measuring systems measure and adjust each angle during bending to ensure consistency in bend angle accuracy, independent of material properties, which is particularly useful when bending parts cut with different grain directions or varying tensile properties.
Safeguarding Operations
In addition to making the operations easier, modern CNC press brakes also prioritize safety. Safety camera systems not only provide a point of operation safeguard but also help ensure that the correct tooling is being used. If the camera system detects the wrong tooling, the system will automatically produce a tooling error, preventing any potential accidents or mishaps. Additionally, a bending line laser projects a visible laser line directly centered on the v-die opening to assist the operator in visualizing the location of the bend angle on the part before bending, making it easier to achieve accurate results.
Achieving More with Less
The combination of modern control interfaces and innovative smart technologies embedded within the machine control makes learning and operating modern CNC press brakes very simple. Utilizing modern CNC press brake technologies and control software technologies in unison as a process, results in increased productivity with less labor time, higher quality with a lower skill set, and increased capacity with fewer press brake machines.