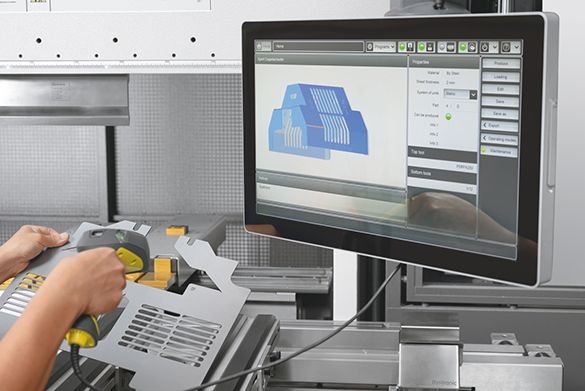
Blog Utilizing Modern CNC Bending Technologies
Offline press brake programming
Offline programming has freed the requirements of press brake operators needing to be trained in part programming and has also freed the machine control of becoming an expensive programming station. The press brake is now free to produce more parts per day.
Initial press brake setup
If required, bend re-sequencing can be achieved by dragging and dropping a bend step before or after another, directly at the control. Scanning of the laser engraved part ID code has enabled the error-proof loading of correct part programs. Graphical tool mapping displays show the operator exactly where each tool needs to be loaded and which type of tooling is to be used. LED mapping on the upper ram shows exactly where the tooling needs to be positioned.
Press brake bending operations
3-D graphical simulations of the bending sequence prior to bending allow the operator to visualize the bending process beforehand. CNC back gauge axes are also graphically displayed in the case where a specific part of the back gauge is being used for part positioning. Arrows indicate when a part needs to be flipped for subsequent bends. Safety Camera systems not only provide a point of operation safeguard, but they also provide safety by applying the correct tooling. If the camera system detects the wrong tooling inserted for the bend operation, the system will automatically produce a tooling error.
A laser bending line projects a visible laser line directly centered to the v-die opening to assist operators with visualizing the location of the bend angle on the part prior to bending. This is especially useful when the part is covering a large portion of the lower v-die and is difficult to visualize the exact bend location.
‘Smart’ technologies make for ‘Smart’ press brakes
‘Smart’ technologies are built into today’s modern CNC press brakes that not only directly impact the quality of the finished parts but the experience level required of the operator. With these smart technologies, the experience no longer resides with the operator, but within the machine itself. For example:
- Automatic dynamic crowning ensures that your angles are consistent along the entire bend length.
- Thickness detection accounts for material thickness deviations and automatically re-calculates the new bottom dead center of the bend angle.
- Mechanical compensations also include frame deflections which can vary depending on the applied tonnage and also temperature compensation for the hydraulic system as it affects the frame over time with varying temperatures. These compensations are applied dynamically during the bending process without operator intervention.
- Laser angle measuring systems measure and adjust each angle during bending to ensure consistency in bend angle accuracy independent of material properties. This is especially useful when bending parts that have been cut with different grain directions or varying tensile properties.
Achieving more press brake productivity with less…
The combination of modern control interfaces combined with innovative ‘smart technologies” embedded within the machine control, makes finding new press brake operators much easier and more productive from the very start. Utilizing modern CNC press brake technologies and control software technologies working in unison as a process will achieve more with less; more productivity with less setup time, more quality bending with less experience, increased available bending time with fewer machines.