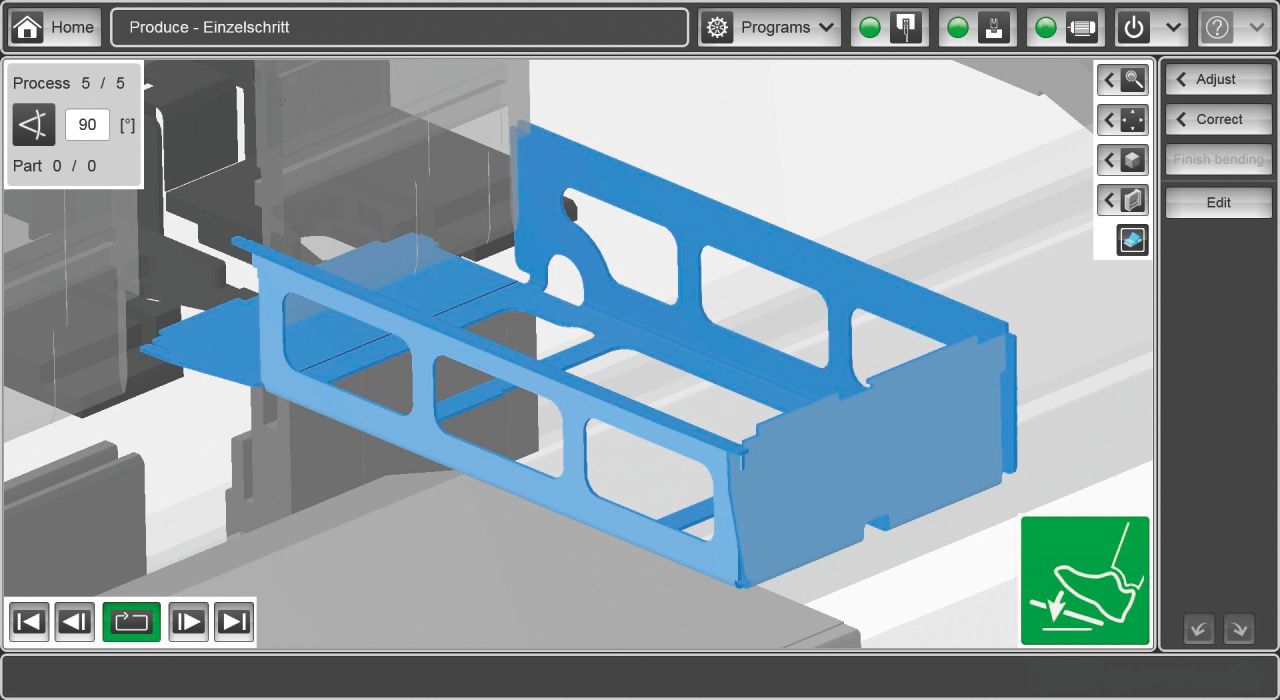
Blog Making a Difference with Modern CNC Controls
Modern CNC control software makes learning to operate today’s complex machinery faster and easier, enabling operators to be productive almost immediately. Attracting qualified young people to the metal fabrication industry is hard enough, so why not entice them with the latest modern CNC software and touch screen interfaces?
Today’s advanced technology continues to forge new paths that accomplish tasks faster and better than ever before. Today’s high-end fabrication machinery has built-in ‘smart’ knowledge that’s been incorporated directly into the machine’s software by the equipment manufacturer. The bottom line is that you no longer need to hire only experienced operators. Within a day or two new operators can be taught to the level necessary to be productive operators. For the most part, ‘old-school’ knowledge has been incorporated into the modern CNC control software that drives the machines, shortening the learning curve.
Operating machine controls that reflect current interfaces such as touch screens and other features found on today’s modern smartphones/tablets is an enticing start. CNC control software capabilities are often influential factors when a prospective candidate decides whether or not to accept or decline a position as a CNC machine operator. They would rather work with modern CNC control technologies as opposed to outdated ones.
Depending on the current cut program, the ability to adapt cutting technologies without having to go back to the programmer is key. CNC-controlled functions that can be applied directly by the operator include setting micro-joints to features that tip up during the cutting process and setting different cutting conditions to features that require it. Control functions such as re-starts from where it last cut a specific part or a specific contour within the part, can be visually accomplished by selecting on the graphics screen the feature or part where you want to restart. The operator can also utilize the control while in operation to program remnant sheets for hot part orders or for adding additional parts to a nest.
Edge detection automatically adapts the program to the orientation of the sheet as it was loaded, eliminating parts running off the sheet edges. The crossjet function allows the operator to automatically apply a piercing fluid and air jet to help eliminate the pierce material from the top of the pierce location. For new materials that are not part of the parameter library, the Parameter Wizard helps operators find the ideal parameter in minutes vs hours. Control functions such as kerf scan and cut control can automatically monitor the cut conditions and make dynamic adjustments to the parameters and also replace and re-center the nozzle automatically.
For press brake operators, there are ‘smart’ technologies that are built into modern CNC press brakes that directly impact not only the quality of the finished parts but the experience level required of the operator. With these ‘smart’ technologies, the experience no longer resides with the operator, but within the machine itself. For example:
- Automatic dynamic crowning ensures that your angles are consistent along the entire bend length.
- Thickness detection accounts for material thickness deviations and automatically re-calculates the new bottom dead center of the bend angle.
- Mechanical compensations also include frame deflections which can vary depending on the applied tonnage and also temperature compensation for the hydraulic system as it affects the frame over time with varying temperatures. These compensations are applied dynamically during the bending process without operator intervention.
- Laser angle measuring systems measure and adjust each angle during bending to ensure consistency in bend angle accuracy independent of material properties. This is especially useful when bending parts that have been cut with different grain directions or of varying tensile strength properties.
- Tooling type can be identified directly by the control and located directly on the ram by LED lights.
- The part orientation and step-by-step bending sequence are displayed graphically in 3D to the operator thereby reducing the possibility of bending errors.
The next time you are looking for a sheet metal cutting or bending machine, remember to spend some time looking closely at the control software. Don’t just look at the offline programming software. look at the embedded software systems and controls that drive the machine and make it easy to operate. Software and controls make all the difference in getting from the order to the finished product in a timely, and efficient manner. They can also make the hiring process much easier.