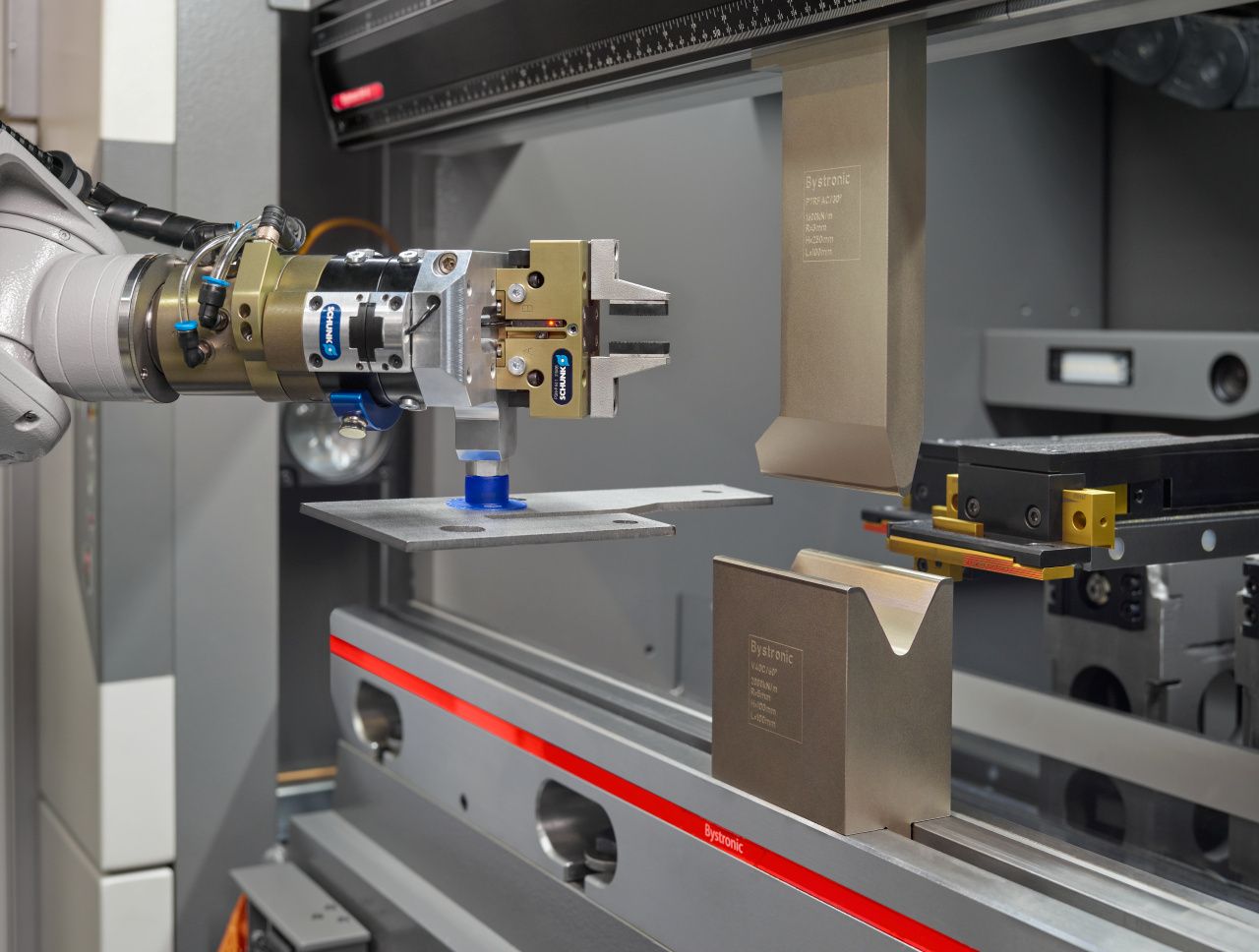
Blog Maximizing Press Brake Capacity with Automation
However, this increase in efficiency has highlighted a pressing need: enhanced bending throughput and capacity to match the laser's speed. While offline programming has freed up some press brake capacity, many manufacturers still find themselves needing further optimization. One of the most effective solutions lies in press brake automation.
Keeping Pace with Fiber Lasers and High-Speed Press Brakes
Press brake automation is as diverse as the applications it serves, offering solutions for various industries and production needs. As fiber lasers and high-speed press brakes achieve cutting and bending speeds of up to one inch per second, maintaining pace becomes increasingly challenging for human operators. Automated press brake systems not only match this speed but also ensure long-term consistency, minimize errors, and eliminate the risks associated with operator fatigue. By integrating automation, manufacturers can maintain peak productivity levels while reducing the physical demands on their workforce.
Fixed Press Brake Automation for Heavy-Duty Applications
For handling heavier and larger parts that typically require multiple operators, fixed press brake automation offers a compelling solution. These automated systems eliminate:
- Operator fatigue associated with prolonged handling.
- Potential injuries during repetitive tasks.
- Inconsistencies in part quality due to human error.
Fixed automation systems are ideal for low-mix, high-volume environments, where they excel in bending parts of similar shapes and sizes. Running these systems around the clock ensures high production output and reliability. Advances in offline robot cell programming now make it faster and easier to program these systems, allowing them to adapt to high-mix operations as well.
Mobile Press Brake Automation for Flexibility
Unlike fixed systems, mobile bending cells offer the flexibility to alternate between manual and automated operations. For example, during daytime shifts, operators can manually handle complex or small-batch tasks. During off-shifts or weekends, these cells can switch to fully automated production, maximizing machine usage.
Recent innovations in programming have reduced setup times significantly, with robot cell programming taking as little as one minute per bend. This efficiency allows mobile systems to handle high-mix, low-volume operations with ease, making them perfect for smaller, light-gauge parts.
Unlocking Off-Shift Productivity
One of the greatest advantages of press brake automation is its ability to increase throughput during off-shift operations. Running automated systems overnight or during weekends can significantly expand bending capacity without the need for additional labor.
This capability allows manufacturers to:
- Utilize equipment during non-peak hours.
- Meet rising production demands without expanding shifts.
- Lower costs per part by increasing overall efficiency.
With automation in place, operators can focus on higher-level tasks such as managing material flow, programming, and overseeing multiple bending cells.
Streamlining with Quick-Change Press Brake Tooling
Another critical area for improvement lies in reducing press brake setup times. This can be achieved through hydraulic tool clamping combined with quick-change segmented tools. These tools offer:
- Front-loading capabilities: Simplify and speed up tool alignment and installation.
- Automatic tool changes by robots: Reduce downtime and improve efficiency.
By accelerating the tooling process, manufacturers can minimize idle time, extend tooling lifespan, and maximize machine output.
Addressing Press Brake Bottlenecks
Managing the volume of work-in-progress (WIP) is essential for maintaining smooth production flows. Bottlenecks at the press brake stage can disrupt schedules, increase costs, and delay customer deliveries. Automation offers the flexibility to:
- Increase bending capacity during peak periods.
- Operate continuously across multiple shifts.
- Meet growing production demands without compromising quality.
By incorporating press brake automation, manufacturers can reduce costs per part, adhere to production timelines, and maintain customer satisfaction.
The Future of Bending Automation
The evolution of press brake automation is reshaping how manufacturers approach bending operations. From fixed systems tailored for heavy-duty applications to mobile solutions designed for flexibility, automation is empowering companies to achieve higher productivity, reduced labor costs, and unparalleled consistency.
As the demand for speed and precision continues to grow, leveraging automation is no longer a luxury—it’s a necessity for staying competitive in the industry. By addressing bottlenecks, optimizing tool changes, and utilizing off-shift capacity, manufacturers can transform their press brake operations into a model of efficiency and profitability.