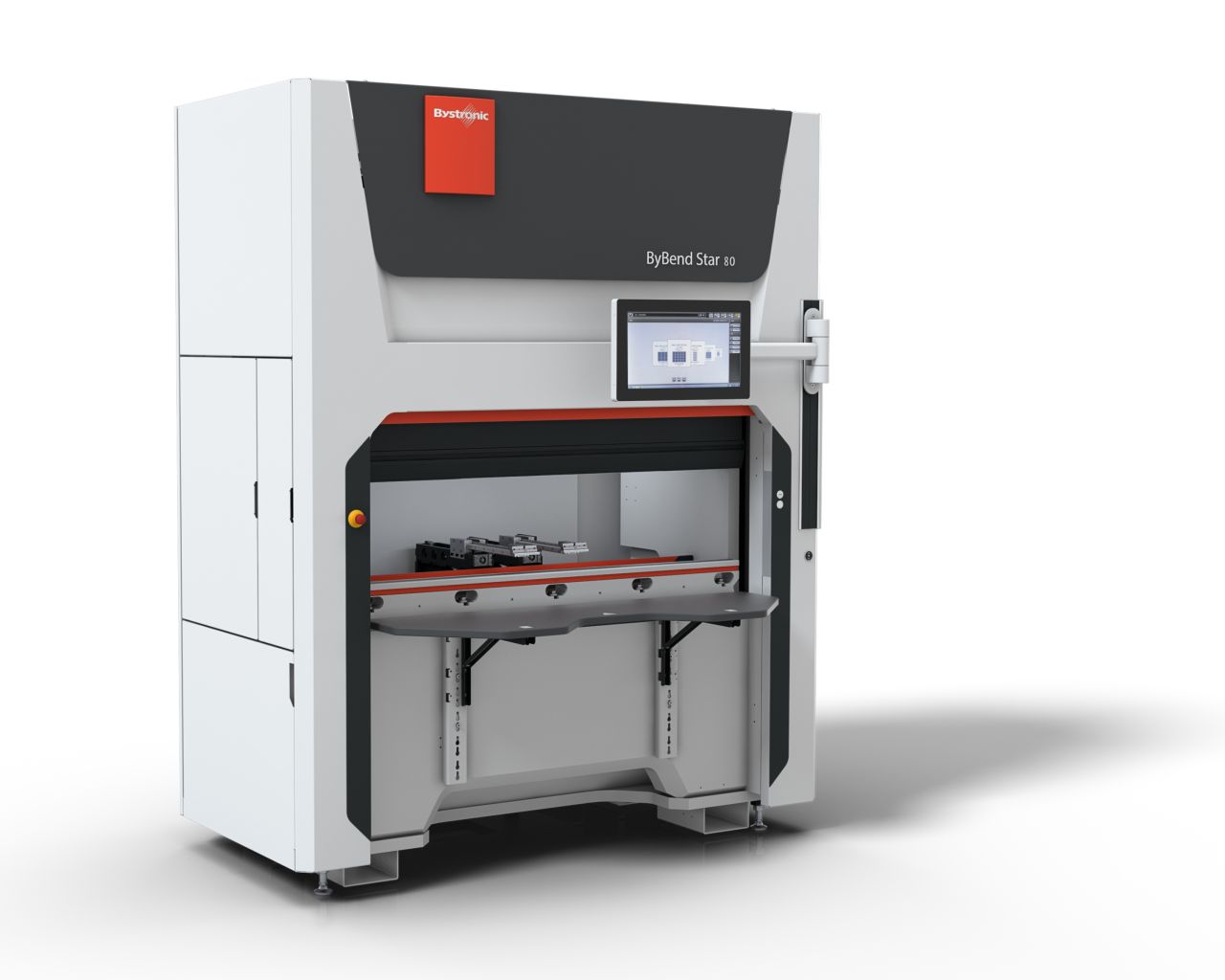
Blog Profiting with high-speed compact Press Brakes
While many companies opt for larger, versatile press brakes to accommodate a diverse range of materials and bending requirements, the ideal choice may lean towards compact high-speed brakes for enhanced productivity.
Press brakes have a specific bending length and a specific tonnage that are suited for the range of parts that each company processes. Companies normally use press brakes that can process a diverse range of materials to maintain flexibility in their production scheduling. Usually, this means having a ten- or twelve-foot bend length and a tonnage that can process from thin to thick. From a scheduling perspective, this is an ideal situation as it provides maximum flexibility in scheduling jobs. But from a productivity and capacity perspective this may not be the ideal situation.
The Physics of Working with Mass
Press brakes come in all different sizes and tonnages and they have vastly different technologies to aid in the bending process. It is possible to process thin small parts on a large tonnage brake. However, it is not possible to process longer thicker parts on a small tonnage brake. The reason is that the longer, thicker parts will most likely exceed the tonnage capacity of the brake. Additionally, running small parts on a large tonnage brake with a long upper ram length is not efficient.
It all comes down to simple physics. A larger, heavier mass is more difficult to accelerate and takes longer to reach top speed than a smaller, lighter mass. Likewise, decelerating a larger, heavier mass is more difficult and will require more time. This all adds up to lost time. Henceforth, small thin parts are more efficiently formed on a smaller press brake.
An Opportunity to Realize Greater Profits
If you find that most of your smaller parts are being formed on oversized press brakes, then this is an area of opportunity to investigate. When you compare to larger press brakes, small brakes such as the Bystronic ByBend Star 40 and 80 ton can process two to three times more parts in the same amount of time. The smaller brake press is faster due to the ability of the machine to accelerate and decelerate both the smaller and lighter upper ram and the smaller back gauge system. This provides not only more throughput capability but also more capacity to bend even more parts on your existing press brakes. Processing smaller, thinner parts on the smaller press brakes is much faster which speeds up the capacity for the larger brakes to process more parts in the larger size range.
The Right Tool for Increased Efficiency
Using the correct press brake on the right applications can not only speed up bending operations but can also create greater machine capacity and flexibility in scheduling. Compact high-speed press brakes can bend up to two times more parts than larger conventional hydraulic brakes. This makes the perfect complement to the production capabilities of a fiber laser. Fiber lasers produce up to 4 times more parts per unit of time. High-speed bending is a major consideration for eliminating possible bottlenecks at the press brake.
Speed and Safety
The next big time-saver comes into play once the press brake starts the active bending program. Wide-view Fast Bend safety cameras enable faster approach, bending, and retract speeds without compromising operator safety. Safely achieve bending speeds of up to 1 inch per second, and approach and retract speeds over 590 inches per minute.
Keeping The Pace
There are opportunities with compact high-speed press brakes that are different for each production environment. Investing in new technology means being able to maintain the pace within your fabrication process as newer fiber lasers are capable of producing higher part volumes. Compact high-speed press brakes can help eliminate these bending bottlenecks.