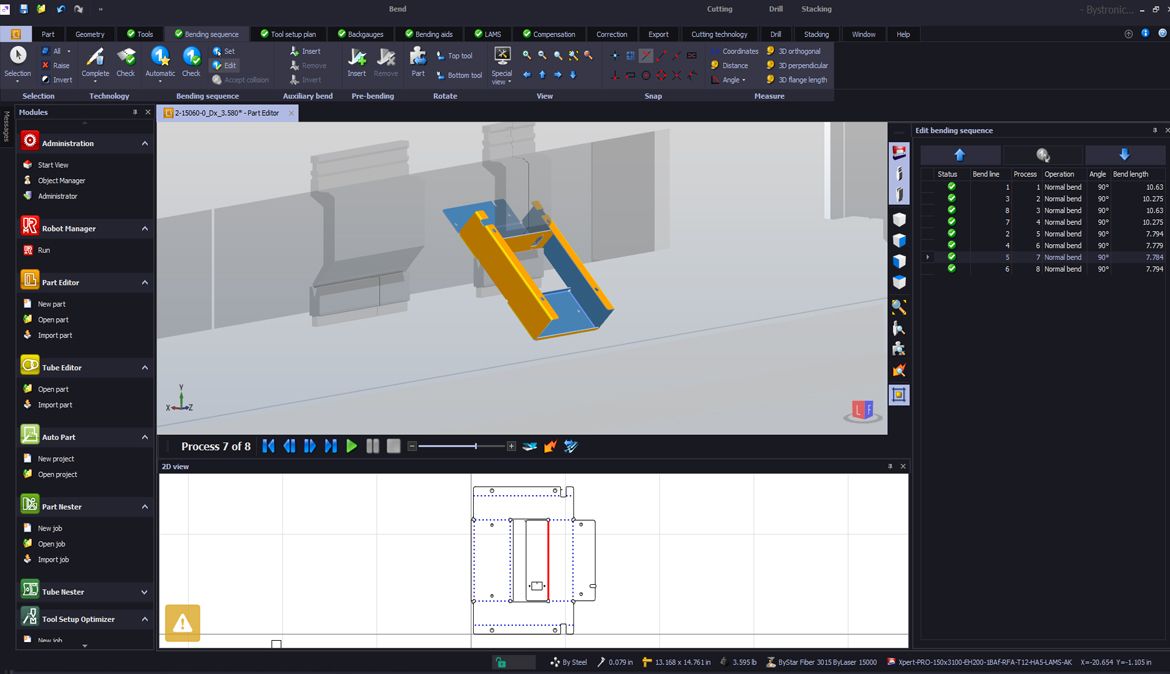
Blog Increase Press Brake Productivity with Off-line Programming
Press brakes, by the nature of their operations in particular, require quite a bit of set-up time due to the different tool setups required and the variety of programs that must be processed each day. The more time an operator spends on set-ups and programming, the less the press brake is available for actual bending. For this reason, it is very important that any and all set-up processes are looked at carefully. The goal is to increase the available bending time and reduce the non-productive process of set-up time.
Off-line Press Brake Programming
While simple parts are most certainly easy to program at the brake, one has to consider the lost bending time when programming directly at the press brake control. If you find that your press brake operators are programming at the machine, you are losing valuable production time.
If you are wondering how you can get more productivity out of your current press brake, and you are not currently off-line programming, this is a great opportunity to make the change. People often see press brakes as the bottleneck of production. This should not be the case! With Fiber lasers cutting parts faster than ever before, it is critical that your downstream processes adapt to the increasing volume of parts.
Implementing off-line programming is a major step towards reducing the non-productive time at the press brake. With off-line programming, as the programmer creates the program either from 3D models or from drawings, the software will select the exact tooling. This determines the application of the correct bend deduction and the overall dimension of the flat blank. The software now calculates the correct flat blank which will be used at the laser, and also the bend program which will be used at the brake. This is critical in reducing setup times because an incorrect flat blank often causes the press brake operator to again make programming changes to the flange lengths in order to compensate for the incorrect blank. Once again, this takes time away from the ability of the press brake machine to actually bend parts.
Additional Off-line Press Brake Programming Benefits
Good off-line programming for the press brake machine will not only select the correct tools and generate bend deductions, but will also set up your tool mapping and automatically set up additional tool stations along the table to accommodate all of the required bends. In addition, the back gauge is simultaneously programmed as each bend is programmed.
The press brake programmer can simulate the bending sequence to make sure there are no collisions before the program is sent to the press brake. Once at the brake, if the operator wishes to change the bending order, they can still do so by utilizing a drag and drop re-sequencing directly on the operator screen. The operator can simulate the final sequence as well before bending.
Optimized Tooling Sequence
With off-line programming, another opportunity to reduce set-up time at the press brake machine is to make sure that the bending programs are sequenced for the least amount of tooling changeovers. All of the programs that require a specific tooling set are placed in sequence, reducing the total number of non-productive times required for tool changes. Off-line programming can provide the optimized sequence of programs for the operator to reduce the total number of tool changes.
An Important First Step
Only after an exhaustive analysis of the non-productive times from the time the order is received until it ships, can a valued assessment of the true impact of reducing set-up time at the press brake machine be made. Reducing set-up time on manually operated press brake machines is one of the most effective ways to increase productivity, increase machine capacity, and reduce overall production costs.