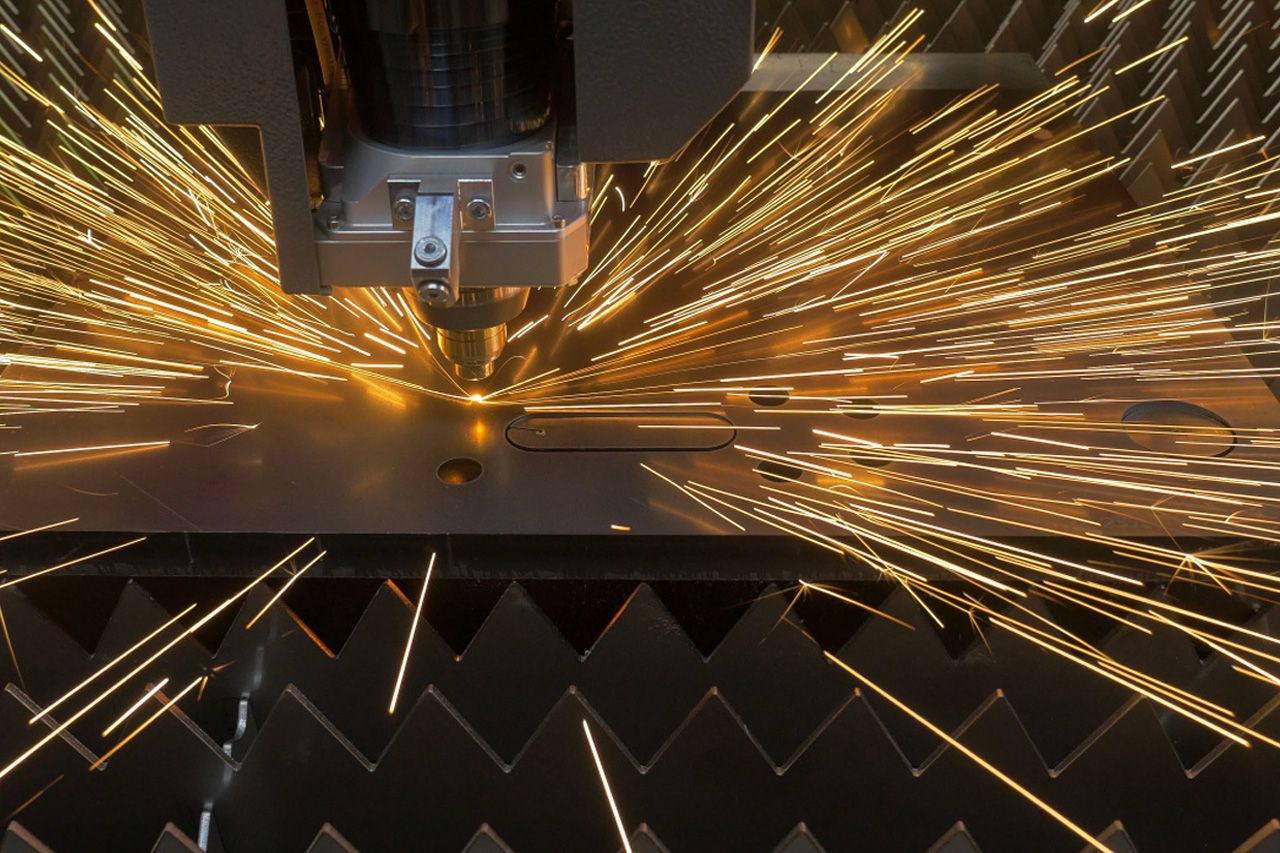
Blog Embracing AI and Advanced Technologies in Fabrication
From optical sensors and machine learning to high-power fiber lasers and automated cutting heads, these innovations are driving substantial progress, enabling manufacturers to meet growing demands for speed, quality, and versatility.
The Rise of AI in Machine Controls
One of the most impactful applications of AI in machine controls is the integration of optical sensors and camera systems. These systems enable real-time monitoring of operational conditions, replacing the need for constant human oversight. Optical sensors, for example, can measure light intensity during laser cutting processes, ensuring that cutting conditions remain optimal and correcting issues on the fly. If a nozzle becomes misaligned or obstructed, the AI-powered system detects this change and automatically stops the machine for an inspection, potentially correcting the issue without operator intervention.
Similarly, machine learning has revolutionized the process of material parameter optimization. In traditional settings, operators would manually adjust cutting parameters when working with unfamiliar materials. Machine learning-driven "parameter wizards" can now automate this process, quickly finding the optimal settings for new materials based on sample cuts. By evaluating results through an iterative process, the system fine-tunes cutting conditions, reducing downtime and ensuring high-quality cuts with minimal human input.
The Evolution of Fiber Laser Cutting Technology
Alongside AI innovations, fiber laser cutting technology has also undergone significant advancements, pushing the boundaries of what’s possible in terms of speed, precision, and material versatility. High-power fiber lasers, particularly those with outputs of 30kW or more, are enabling manufacturers to cut a wider range of materials—from thin sheets to thick plates—more efficiently and accurately than ever before.
One of the primary challenges with traditional fiber lasers, especially when cutting thicker materials like steel, is their small beam diameter. While smaller beams excel in precision cutting of thinner materials, they struggle with thicker plates due to difficulty expelling molten material. However, recent advancements in beam-shaping technologies, like Bystronic’s BeamShaper system, have solved this problem by modifying the beam profile to handle thicker materials more effectively. This innovation allows fiber lasers to achieve cutting speeds and edge quality that were once reserved for CO2 lasers, making them a comprehensive solution for both thin and thick material cutting.
Another breakthrough has been the development of advanced assist gas technologies, such as gas mixing. By blending oxygen with nitrogen, manufacturers can achieve faster cutting speeds and greater thickness capacity while reducing edge burrs and improving material properties, such as paint adhesion. These enhancements are especially valuable in high-power fiber lasers, where the combination of powerful beams and optimized gas mixtures accelerates productivity without sacrificing quality.
Automating the Cutting Process
Both AI-driven machine control systems and modern fiber laser technology share a focus on reducing human intervention and increasing automation. This focus has led to the development of advanced cutting head technologies that combine multiple automated processes to improve cutting accuracy and consistency.
For example, automated nozzle systems can adjust nozzle sizes and perform automatic calibration based on the material being cut. This reduces the need for operators to manually change components or adjust settings, further minimizing downtime. Additionally, systems like kerf scanning continuously monitor the cut channel to detect irregularities and automatically make corrections, such as re-cutting affected areas or recalibrating the nozzle.
These automated systems work hand-in-hand with AI-powered vision and control systems to eliminate variables and ensure consistent cut quality. By removing the need for human intervention in areas like nozzle inspection, calibration, and gas mixing, manufacturers can achieve faster, more precise cuts with reduced operational risk.
The Future of Manufacturing: Seamless Integration
The future of manufacturing is one where AI and advanced laser cutting technologies work together seamlessly to create fully autonomous, highly efficient systems. As both AI and fiber laser technologies continue to advance, the potential for increased automation, reduced operational costs, and improved product quality will only grow.
AI will continue to enhance machine learning algorithms, enabling faster and more accurate parameter optimization across a broader range of materials. Likewise, laser cutting systems will evolve with new innovations in beam shaping, assist gas optimization, and cutting head automation, allowing manufacturers to achieve superior results with minimal oversight.
Ultimately, the integration of AI and fiber laser cutting technologies not only transforms individual machine performance but also revolutionizes entire production lines, providing manufacturers with a competitive edge in an increasingly demanding marketplace.
AI and Advanced Laser Technologies
The intersection of AI and fiber laser cutting technology marks a significant shift in modern fabrication practices. Through enhanced automation, smarter machine controls, and improved cutting capabilities, manufacturers can achieve higher levels of precision, efficiency, and reliability. As these technologies continue to evolve, the future of manufacturing looks brighter, with AI and advanced laser systems playing a central role in shaping the next generation of industrial processes. By embracing these innovations, fabricators can stay competitive, reduce costs, and meet the ever-growing demands of the global market