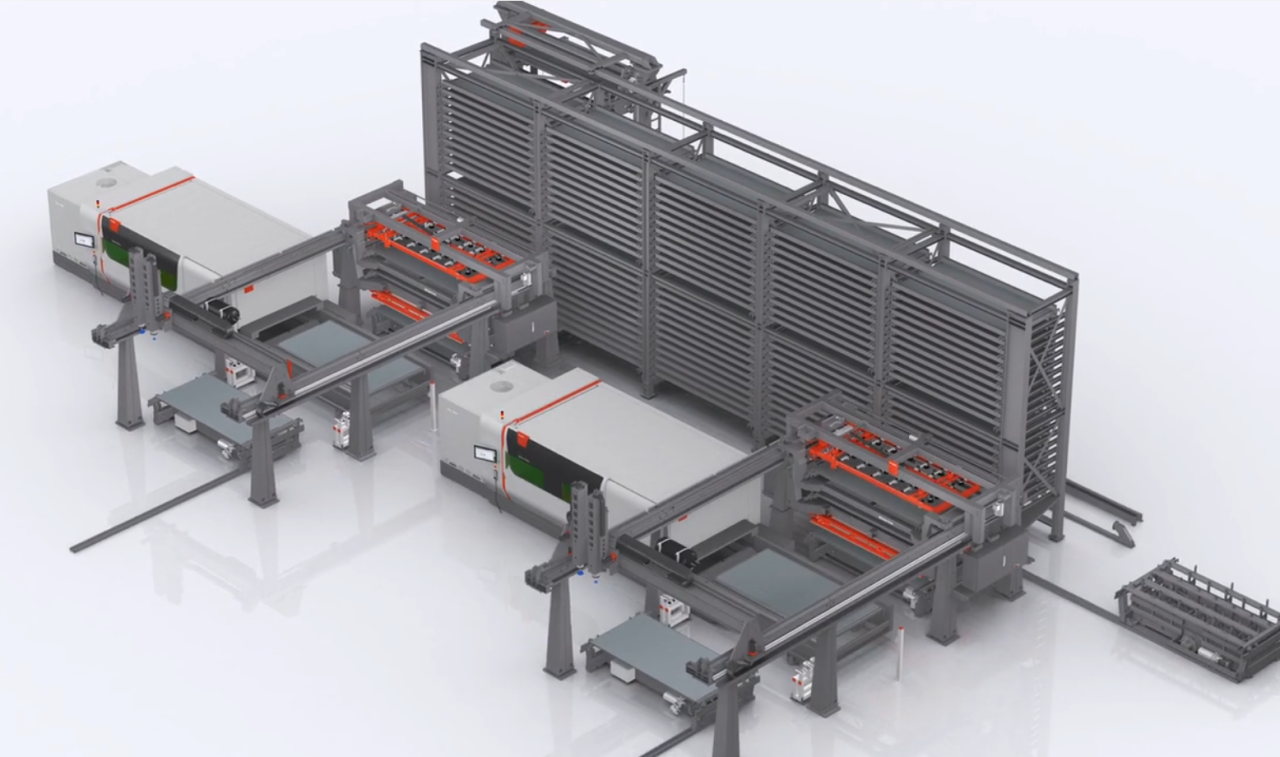
Blog Solving Raw Material Supply Chain Challenges for Metal Fabricators
With costs for raw materials at a premium and deliveries out sometimes weeks, this poses a major problem for fabricators and their customers. With automated material storage systems, raw materials can be purchased in bulk providing a price advantage over traditional single sheet orders, and materials can always be at the ready. The risk of losing an order or even worse a customer, due to delivery or pricing, is an everyday challenge.
With today’s Fiber laser cutting machines and their capability to process a vast amount of sheet metal on a daily basis, maintaining materials at the ready is essential to maintaining a consistent pace of production. For this reason, it is important to have some form of automated material storage and material handling so that the raw materials are cycled to the machine in a timely manner.
Reducing Material Costs
What if you could buy your sheet metal in bulk when material prices are lower and then not only receive a lower price but more than likely a higher discount for a volume purchase? But then where would you store it? Storing it on the production floor takes up a lot of expensive lateral real estate. It is also very inefficient when you need to access the material, especially when it’s located behind another stack of material. The solution is an automated material tower or warehousing system that not only enables you to store bulk sheet metal purchases but also eliminates wasting valuable production floor space. Instead of lateral storage, the materials are stored in vertical towers containing automated shelves. Accessing the materials is just a click away with your automated material tower or warehousing system with delivery directly to the required machine location.
Efficiency and Material Storage
The benefits of automating material storage lay in the efficiency factor: Material storage systems enable the seamless transition of material changes from job to job, reducing non-productive waiting times. How often have you seen a laser cutting machine sitting idle because it doesn’t have the material to process the job? Keeping a machine supplied with the proper materials and in a timely manner is a task that requires precision timing. Often, it is the task of a forklift operator or even the machine operator to make sure the laser has the required materials, but timing is everything and inevitably this leads to inefficiencies and lost production time. Maintaining materials at the ready is essential to maintaining a consistent pace of production and reducing non-productive time.
An Essential Component for High-mix
If you are operating in a high-mix material environment, automating the material storage and handling is essential. Each changeover of material is an opportunity to either maintain your pace of production or add non-productive time. The higher the changeover rate, the higher the risk of production loss due to not having the proper materials supplied to the machine. Today’s modern laser cutting machines are able to gather statistical data on the productivity of the machines and also non-productive waiting times. If you are in a high-mix material environment it is prudent to measure the non-productive waiting times for continuous improvement purposes and to justify material automation.
Competitive Advantage
Maintaining materials ‘at the ready’ with automated material storage systems eliminate inefficiencies when changing materials from job to job and maintains a consistent pace of production. You now have a plan that compensates for fluctuating market condition prices, is able to deliver parts faster and less expensively, is more efficient with material handling, and will most likely win more business.