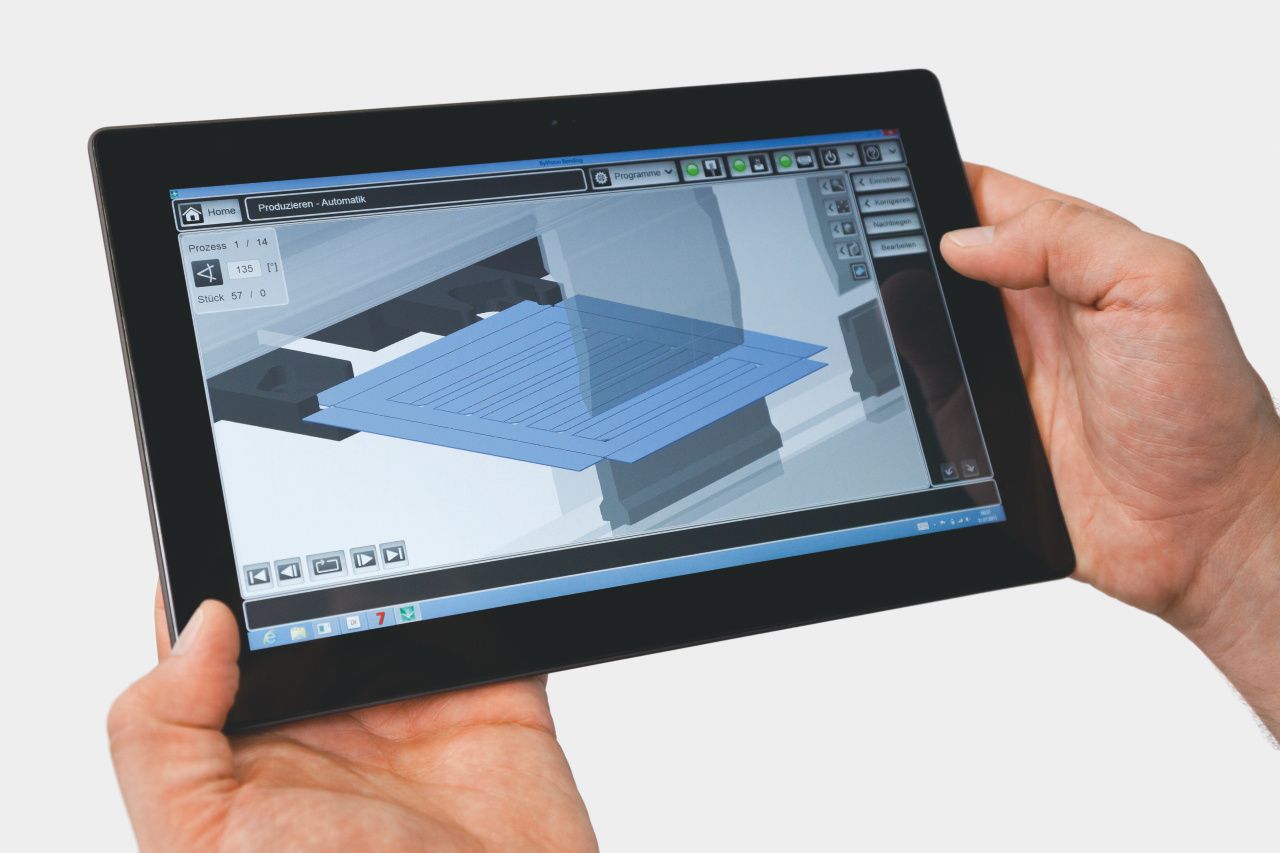
Blog Driving Efficiency with Software Technology
While machines have become more automated so have the software systems that drive front-end order processing, programming, and machine control interfaces.
Managing Orders and Planning
Companies have streamlined the entire order process by using an ERP software interface with their existing ERP (Enterprise Resource Planning) system to streamline incoming orders. In addition, an MES software module (Manufacturing Execution System) provides the ability to plan, monitor, and track all of the active jobs and machine workloads. This enables managers to react on short notice to ever-changing production requirements.
As each job is released to production, the MES software analyzes the order, identifies job requirements such as material type, thickness, and due dates, and organizes them accordingly. Based on required operations, production workflows are assigned to each job. Next, MES calculates the required times for each operation based upon known setup, cycle times, and quantities to be produced, and provides the total estimated production time from start to finish. As each job maintains an effective delivery date, this becomes the basic parameter for the planning and monitoring of the job in real time.
Once a job is scheduled for production, the MES identifies estimated start and finish dates and times for each operation based on machine workloads and the estimated completion date of the job. Jobs that are being pushed outside of the scheduled start and finish times due to current machine workloads are automatically identified and flagged. The MES makes allowances for flexible responses to changes in orders or priorities. Production managers can adapt orders according to changing requirements and machine workloads.
Programming functions can produce part identification QR Codes for laser etching that can then be scanned by smartphones and laser scanners. On-the-spot identification of parts and automatic uploads of the correct programs at the machines provide for greater quality control measures and part traceability.
Control Software
Built-in ‘smart’ knowledge has been incorporated directly into the machine’s software by the equipment manufacturer. The bottom line is that you no longer need to hire only experienced operators. Within a day or two new operators can be taught to the level necessary to be productive operators. For the most part, ‘old-school’ knowledge has been incorporated into the modern CNC control software that drives the machines, shortening the learning curve.
Real-time statistics and monitoring
From the time a sheet metal cutting or metal bending machine is operational, it begins to produce production data. Each system message or error message is effectively a subset of that machine’s processes along with the production data. The machine control software can communicate machine and production data to Overall Equipment Effectiveness (OEE) software systems for production and statistical analysis. The most effective way to measure the production process is with statistical data. This analysis helps manufacturers to streamline production and increase the overall efficiency and effectiveness of their equipment. Measured over a specific period of time, this data can determine where the hidden opportunities might be.
With mobile software applications, smartphones and tablet computers are able to provide real-time data of production CNC machines. Which programs have been processed, which are currently in production, and which have yet to be processed. All with the ability to monitor specific parts and their completion timelines. Machine system messages can also be monitored on a smartphone as well as video feeds from web-enabled, high-definition cameras that allow users to keep a “virtual eye” on the machine without having to physically be there.
Competitive Advantage with Software
While we all recognize the value of new and improved sheet metal fabricating equipment, we sometimes overlook the competitive advantages that are being created by innovative software. Software and controls make all the difference in getting from the order to the finished product in a timely, and efficient manner. Taken together, advances in both machine and software design drive greater productivity and efficiency and provide the competitive differentiation that companies are looking to achieve.