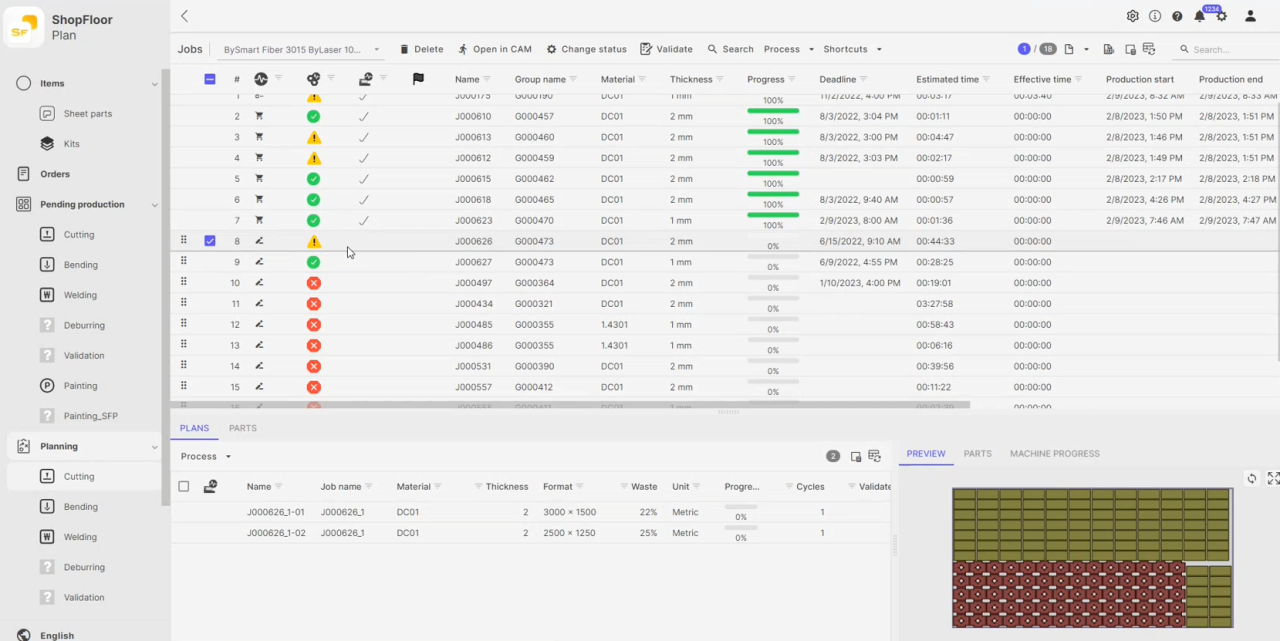
Blog Managing the Big Picture with MES
Utilizing a Manufacturing Execution System (MES), like Bystronic’s ‘BySoft Shop Floor’ software, provides the ability to plan, monitor, and track all of the active jobs and machine workloads and enables managers to react on short notice to ever-changing production requirements.
Thanks to a visual planning interface, you can decide the allocation of job plans to each work center on your shop floor. Balance workloads and reorder priorities, considering the state of your shopfloor and ensuring the delivery of your order commitments.
Preparing the Order
Companies have streamlined the entire order process by interfacing with their existing ERP (Enterprise Resource Planning) system and processing their parts automatically from incoming orders to finished parts. BySoft Shop Floor can identify incoming production orders and their requirements, and in synchronization with a CAM module, automatically program the parts, nest, and schedule to the appropriate machines. Scheduling can be defined based on the due date or job priority. To take advantage of material utilization with similar parts, the triggering of a job can be delayed until the clearly defined, latest possible point in time while still guaranteeing assured delivery deadlines. The cutting plans can be automatically released to the machines based on achieving the required material yields. This leads to more parts per sheet, better material utilization, and better delivery forecasts.
Analyzing in Real-time
As each job releases to production, the MES analyzes the order and identifies job requirements such as material type, thickness, and due dates, and organizes them accordingly. Based on required operations, production workflows are assigned to each job. Next, MES calculates the required times for each operation based on known setup, cycle times, and quantities to be produced, and provides the total estimated production time from start to finish. As each job maintains an effective delivery date, this becomes the basic parameter for the planning and monitoring of the job in real time. Once a job is scheduled for production, the MES identifies estimated start and finish dates and times for each operation based on machine workloads and the estimated completion date of the job. Jobs being pushed outside the scheduled start and finish times due to current machine workloads are automatically identified and flagged. The MES makes allowances for flexible responses to changes in orders or priorities. Production managers can adapt orders according to changing requirements and machine workloads to load balance their production.
Flexibility in Routing
Real-time data from each machine provides actual runtime for comparison to target times for each job. The actual production time adjusts the job completion date in real time and is monitored by the MES. Unscheduled delays affecting the job completion date are flagged. Declining machine performance is identified in real-time and acted upon immediately by the operator or by maintenance. Re-routing of jobs to an alternate machine is done on-the-fly to maintain optimal production schedules. Production information such as the current operation of the job within the workflow, how many parts have been produced, and the expected completion of the job are identified from within the MES.
Managing in Real-time
Manufacturing Execution System (MES) software enables companies to plan, monitor and track all steps within the manufacturing workflow for any given order. This is made possible by the interconnectivity of machines and the real-time data generated by each machine. The use of MES software has greatly enhanced the ability of manufacturers to dynamically respond to changes in orders, prioritization, and workflow capacities while maintaining production schedules. The Bystronic BySoft Shop Floor MES allows management of Bystronic laser cutting (sheet parts and tubes) and bending machines, third-party machines, as well as manual manufacturing processes, e.g. drilling, refurbishing, painting, welding, assembling, packaging… This enables you to manage your entire end-to-end production process.