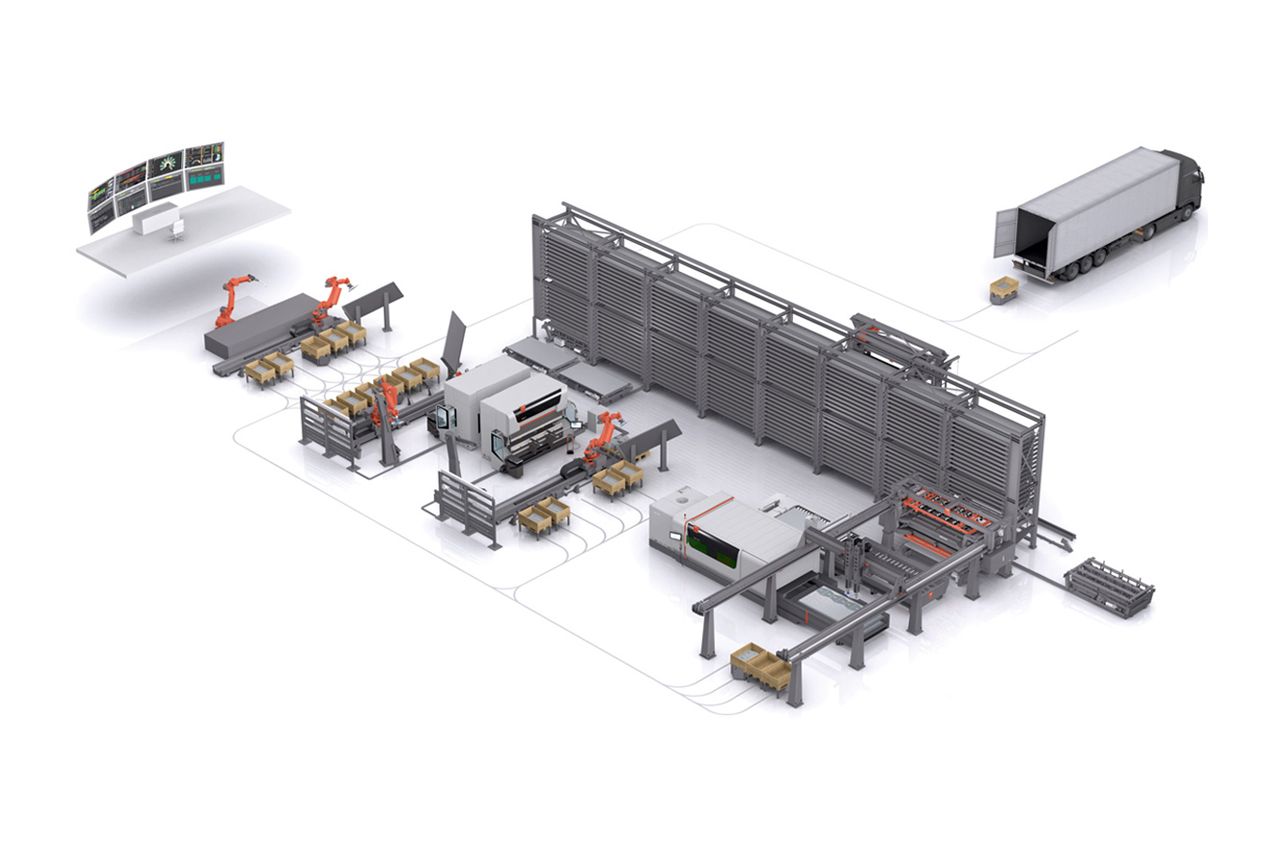
Blog Improving Fabrication Workflows with Modern Technologies
Fabrication businesses face the challenge of maximizing operational efficiency while minimizing costs and processing times. Two key approaches to achieving these goals are digitalization and automation, paired with robust data analysis. By harnessing these tools, companies can not only streamline their workflows but also make more informed, objective decisions that drive continuous improvement and profitability.
The Role of Digitalization and Automation in Streamlining Workflow
From order entry to product delivery, every stage of the fabrication process can be optimized through digitalization and automation. These technologies reduce the time spent on non-value-added activities, which is crucial in industries where speed and accuracy are essential for competitive advantage. The shift from paper-based systems to digital order management, for instance, is one of the first steps in streamlining operations.
Digitalizing the front-end order process allows for smoother workflows. Orders can be placed electronically via online portals or electronic data interchange (EDI), eliminating manual data entry and reducing the risk of errors. Once entered, the order details—such as invoices, shipping labels, and purchase orders—are stored electronically. This eliminates the need for physical paperwork, enhancing organization and accessibility.
Furthermore, digital reporting tools enable companies to generate and share key business metrics, such as order status, inventory levels, and machine performance, all in real time. This ease of access to data empowers managers to make quick, informed decisions, whether they’re adjusting production schedules or reallocating resources.
Automation: Key to Maximizing Machine Efficiency
Modern fabrication machines are designed to handle complex tasks quickly and with high precision. However, without a properly integrated material handling system, even the most advanced machines can experience idle time, undermining the efficiency of the investment.
Material automation ensures that raw materials are consistently available when needed. As one sheet is processed, automation prepares the next, while unloading finished products simultaneously. This seamless operation minimizes downtime and helps maintain optimal machine cycle times. The ability to keep machines running efficiently is a primary contributor to reducing overall production times and increasing throughput.
Reducing Non-Productive Time
In any manufacturing process, non-productive time is an inevitable challenge. These are the moments when equipment is idle or waiting for materials, and they can eat into valuable production hours. By tracking and analyzing non-productive times, companies can pinpoint inefficiencies and take steps to eliminate them.
For example, soft processing times—such as order entry, production planning, and engineering—can significantly impact overall production time. Often overlooked, these stages can be digitized and automated to minimize delays and improve overall workflow. By using digital tools like Enterprise Resource Planning (ERP) and Manufacturing Execution Systems (MES), businesses can coordinate tasks more effectively and respond swiftly to changes in production requirements.
Objective Decision-Making with Machine Data
While digitalization and automation improve the workflow, objective decision-making plays a pivotal role in ensuring that these technologies deliver long-term value. The key to making informed decisions is data—specifically, machine and production data.
Machine data provides insights into various aspects of equipment performance, including processing time, downtime, and part quality. One of the most effective ways to assess this data is through Overall Equipment Effectiveness (OEE) metrics. OEE is a comprehensive measure that evaluates a machine’s performance based on its availability, speed, and quality output.
- Availability measures the proportion of time the machine is actually running versus planned downtime.
- Performance gauges how quickly the machine is running compared to its maximum speed.
- Quality evaluates the percentage of good parts produced relative to the total number of parts.
By analyzing these metrics, managers can identify inefficiencies, such as excessive downtime, performance lags, or quality issues. With this data, proactive measures can be taken to reduce waste, optimize machine usage, and ultimately improve production efficiency.
Real-Time Data and Continuous Improvement
One of the most valuable aspects of modern manufacturing technology is the ability to collect and analyze real-time data. Smart manufacturing software integrates with machines to provide continuous performance tracking, which not only helps identify inefficiencies but also supports ongoing improvement efforts.
For example, real-time monitoring allows managers to compare standard benchmarks with actual machine performance and identify discrepancies as they occur. When an issue arises—such as a machine operating below expected performance levels—corrective action can be taken immediately, preventing further delays or production losses. This rapid response capability is critical in today’s fast-paced market, where even minor delays can result in lost orders and diminished customer satisfaction.
As real-time data accumulates over time, businesses can identify trends and areas for continuous improvement. This information fuels long-term decision-making, whether it’s investing in new equipment or adjusting operational strategies to better meet customer demands.
Embracing Modern Technologies
In the competitive world of fabrication, companies that embrace digitalization, automation, and data-driven decision-making position themselves for success. By streamlining workflows, optimizing machine performance, and using real-time data to make objective decisions, businesses can significantly reduce production times, cut costs, and improve overall efficiency. With the ability to analyze and act on machine data, manufacturers can not only enhance their current operations but also ensure sustained growth and profitability in an increasingly demanding industry.