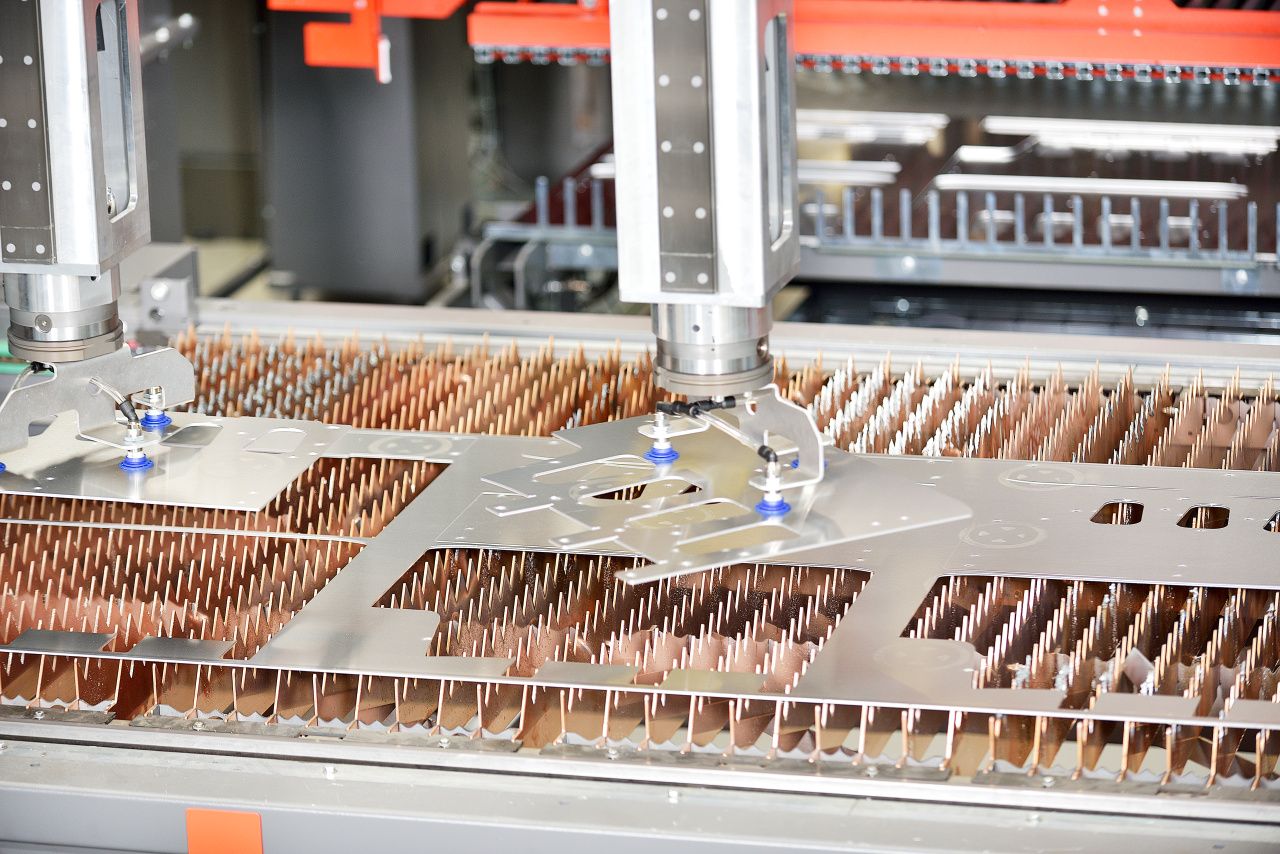
Blog Optimizing Material Handling in the Fabricating Value Chain
Machines without automated material handling often experience inconsistent production cycles due to delays in material availability or bottlenecks during part removal.
If you analyze machine data, you’ll likely see substantial idle or waiting times, often caused by delays in supplying raw material or removing finished parts from the cutting bed. These inefficiencies not only reduce throughput but also increase overall production costs. By addressing these inefficiencies, you can improve material handling and unlock significant productivity gains.
Supplying raw materials: Automating the flow
Once the cutting program is released to the laser machine, the efficiency of your material supply process becomes crucial. Does your system rely on manual intervention to retrieve raw materials? In many traditional setups, this step involves an operator retrieving raw material from storage, using a forklift to transport it to the machine. For each material changeover, valuable time is wasted, especially in high-mix environments where there are frequent changeovers throughout the day.
This is where automated material storage and retrieval systems (AS/RS) come into play. Such systems can store multiple types and thicknesses of material, automatically retrieving the correct material as needed. When integrated with your laser cutting machines, the AS/RS can deliver the next material even while the current sheet is still being processed. This reduces idle time between material changes and ensures that production continues with minimal interruption.
Key benefits of automated material storage systems:
- Reduced wait times: Materials are delivered to the machine before the previous job is completed, eliminating idle periods between jobs.
- Increased machine utilization: The laser is continuously supplied with materials, allowing it to operate at full capacity without delays caused by manual material handling.
- Error reduction: Automated systems reduce the risk of human error, such as retrieving the wrong material or delays in material transportation.
Automating the material loading process: Increasing efficiency
Once the raw material is delivered to the laser cutting machine, the next step is loading it onto the cutting bed. Manual loading can be slow and inefficient, especially when multiple sheets need to be processed in quick succession. Automating the loading process eliminates the need for human intervention and ensures that materials are loaded seamlessly.
With automated loading systems, the next sheet of material is prepared on a secondary shuttle table while the machine is cutting on the primary table. This “dual-table” system minimizes downtime between cuts. The moment the laser finishes cutting on the primary table, it switches to the secondary table, where the next sheet is already loaded and ready to go.
Additional opportunities for automation
- Smart sequencing: Automated software systems can prioritize urgent jobs or combine orders that use the same material type, further optimizing material usage and reducing processing time.
- Remote monitoring and control: Advanced software systems allow operators to monitor material flow and machine performance remotely, enabling proactive management of potential bottlenecks or material shortages.
Automating the cut parts unloading process: preventing bottlenecks
The unloading process is often a major bottleneck, and it is just as critical as loading and cutting. If parts are not unloaded in a timely manner, the entire production process grinds to a halt. Automating the unloading process is essential to maintain the flow of production.
There are two main approaches to automating the unloading process:
- Unload fork systems: These systems remove the entire cut sheet from the machine, parts and all, in a single operation. While this is more efficient than manual unloading, it still leaves the task of sorting and stacking parts.
- Automated sorting systems: A more efficient approach is to sort individual parts from the sheet as they are unloaded. Automated sorting systems can categorize parts by order, size, or material type, stacking them in neat, organized piles for the next stage of the production process. The system can also remove the scrap skeleton once all parts are sorted. This reduces manual sorting time, prevents errors, and ensures that similar parts are stacked together for easy retrieval.
Material handling for downstream processes
As most automated fiber laser cutting systems run multiple shifts so must the downstream machines like bending and welding systems. Automated bending cells make use of highly integrated robots that can not only load raw materials from the material stacks but can also change tooling and grippers, orient and grip the parts, process through the bending cycles, and then stack the finished parts.
The beauty of these automated systems is that once they are set up they can run across multiple shifts and on weekends with little to no supervision. Part movements can be automated by autonomous guided vehicles (AGVs) that basically move finished part skids from laser cutting to bending, to welding and paint stations without forklift material movers.
Reducing bottlenecks: A data-driven approach
By focusing on automating both the material supply and part removal processes, manufacturers can significantly reduce bottlenecks. However, it’s important to note that variability in these processes is often not accounted for in job quotes. This can lead to missed deadlines and dissatisfied customers, as unanticipated delays affect production schedules. Tracking and analyzing the waiting times and idle periods for each job will provide valuable data for making informed decisions on where to invest in automation.
Beyond reducing waiting times, automation improves consistency and reliability. Fewer manual steps mean fewer opportunities for mistakes and more predictable production timelines. Companies that implement automated systems often see a direct impact on their ability to meet or exceed promised delivery dates, resulting in higher customer satisfaction.
By keeping an open mind to new technologies and processes, your business can not only streamline current operations but also reimagine how the entire fabricating process could look in the future. The key to success is not just improving the process as it exists today but having a vision of what it can become with the right advancements.