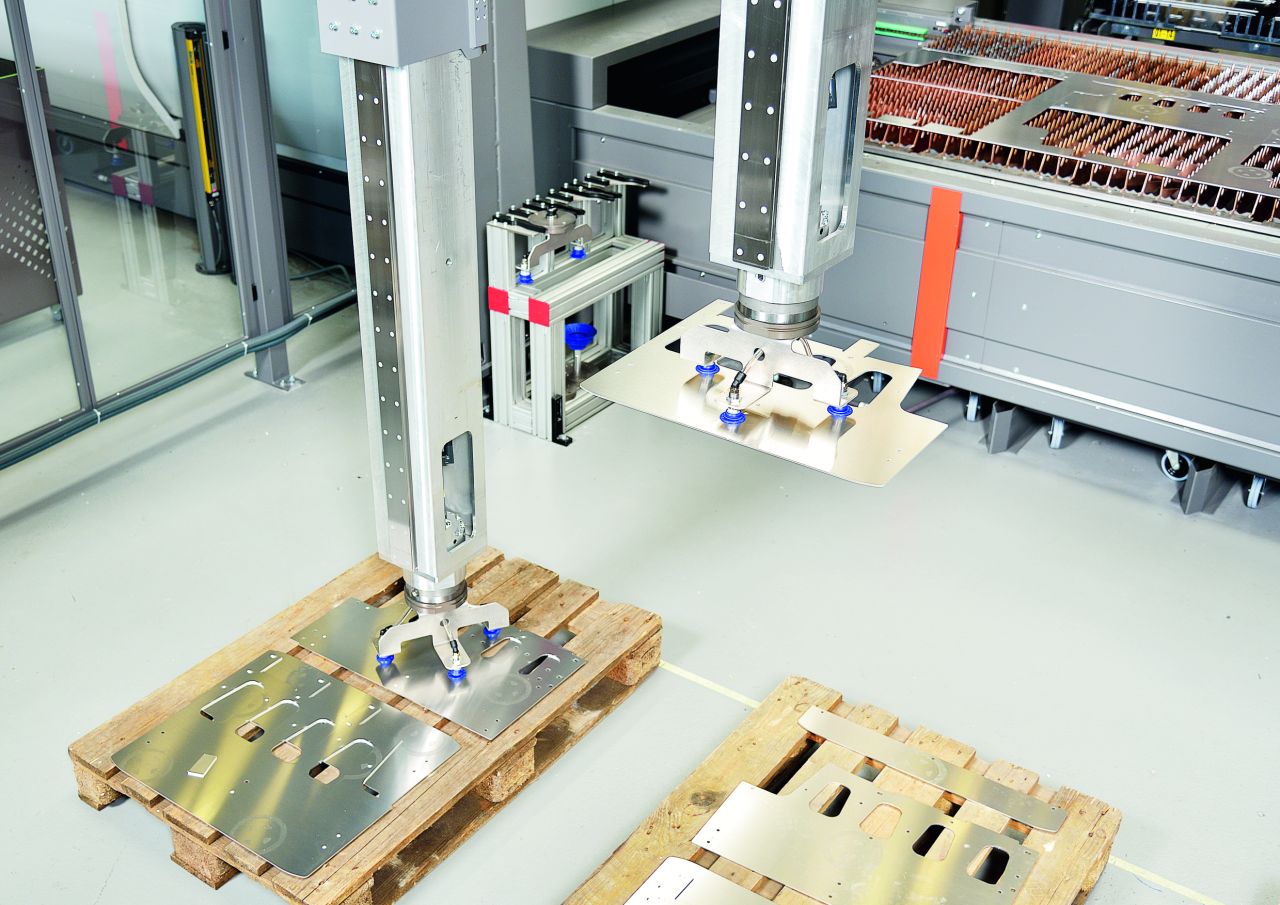
Blog Eliminating bottlenecks with Material Handling
These bottlenecks, characterized by interruptions and delays, can severely impact production timelines and overall operational effectiveness. Recognizing this challenge, incorporating material handling automation has emerged as a pivotal solution, transforming the way laser cutting systems function and optimizing the entire fabricating value chain.
At the heart of this issue lies the loading and unloading process with laser cutting systems. Machines lacking material handling automation exhibit significant variability in production time, especially during these crucial stages. The waiting or idle times, meticulously recorded from the laser cutting machine’s data, clearly indicate the presence of these bottlenecks. These waiting times stem from two primary factors: the absence of raw materials supplied to the machine or the failure to unload cut parts before the machine completes processing the previous sheet. Addressing these bottlenecks at this pivotal juncture in the fabricating process is paramount, as it directly influences downstream operations and the overall process times.
Automating the supply of raw materials to the laser cutter
Automation enters the scene as a game-changer, particularly in material supply. Consider the scenario when cutting programs are released to the laser cutting machine for processing. In traditional setups, human intervention is required to retrieve raw materials from a storage area, often utilizing a forklift. The time accumulated in performing this action for each material changeover can be substantial, especially in high-mix environments with frequent daily changeovers. This manual intervention becomes a critical bottleneck.
However, with an automated material storage system in place, this bottleneck is effectively eliminated. Multiple material types and thicknesses can be supplied seamlessly across various machines. The beauty of automation lies in its ability to seamlessly communicate with the laser cutting machine. As programs are released, communication with the material storage system is automatic, and the subsequent material order can be delivered while the machine is still processing the last sheet of the previous order. This synchronized movement of raw materials ensures a continuous supply, eliminating waiting times and optimizing production efficiency.
Automating the laser cutting machine material loading process
Automation plays a pivotal role in the material loading process. Once the laser cutting machine is presented with the raw material stack, automating the loading process becomes imperative. In an automated setup, loading the material is an integral part of the automatic sequencing tied to the machine’s material request. No longer does one need to wait from sheet to sheet or from order to order. Sheets are efficiently loaded onto secondary shuttle tables while the laser cutter is seamlessly cutting on the primary table. However, a crucial sequence must occur between loading and unloading: the timely unloading of cut materials. Failure to unload the cut material promptly results in accumulating waiting times, disrupting the flow of operations.
Automating the laser cutting machine material unloading and parts sorting process
Here enters the significance of automating the material unloading and parts sorting process. Automating the material unloading process is not just desirable but crucial. It is the linchpin upon which the loading and cutting processes hinge. Without timely unloading, a bottleneck is created, impeding the entire workflow. Addressing this challenge necessitates a thoughtful approach. Two methods of practice: unloading the entire cut sheet with parts using an unload fork system or having the parts unloaded and stacked using an automated sorting system for the parts and a fork system to remove the material skeleton when completed.
The system involving automated sorting proves to be efficient and transformative. The automated system separates cut parts from the sheet material based on the order they belong to. Similar parts are organized into neat stacks for subsequent fabricating processes. By reducing manual intervention and minimizing errors in stacking similar part revisions, the automated sorting system significantly reduces process times, enhancing efficiency and throughput.
Tangible benefits to the sheet metal fabrication business
By identifying, addressing, and eliminating material handling bottlenecks, sheet metal fabricators can pave the way for unparalleled efficiency, heightened profitability, and sustained business growth. By mitigating these bottlenecks, fabricators can deliver on their promises with greater precision, ensuring that customer delivery dates are met consistently. This newfound precision not only enhances operational efficiency but also bolsters profitability. Inaccurate job quotes, a common consequence of overlooking these material handling bottlenecks, can erode profits significantly. By addressing these variabilities and accurately reflecting them in job quotes, businesses can maintain healthy profit margins, contributing to long-term sustainability and growth.