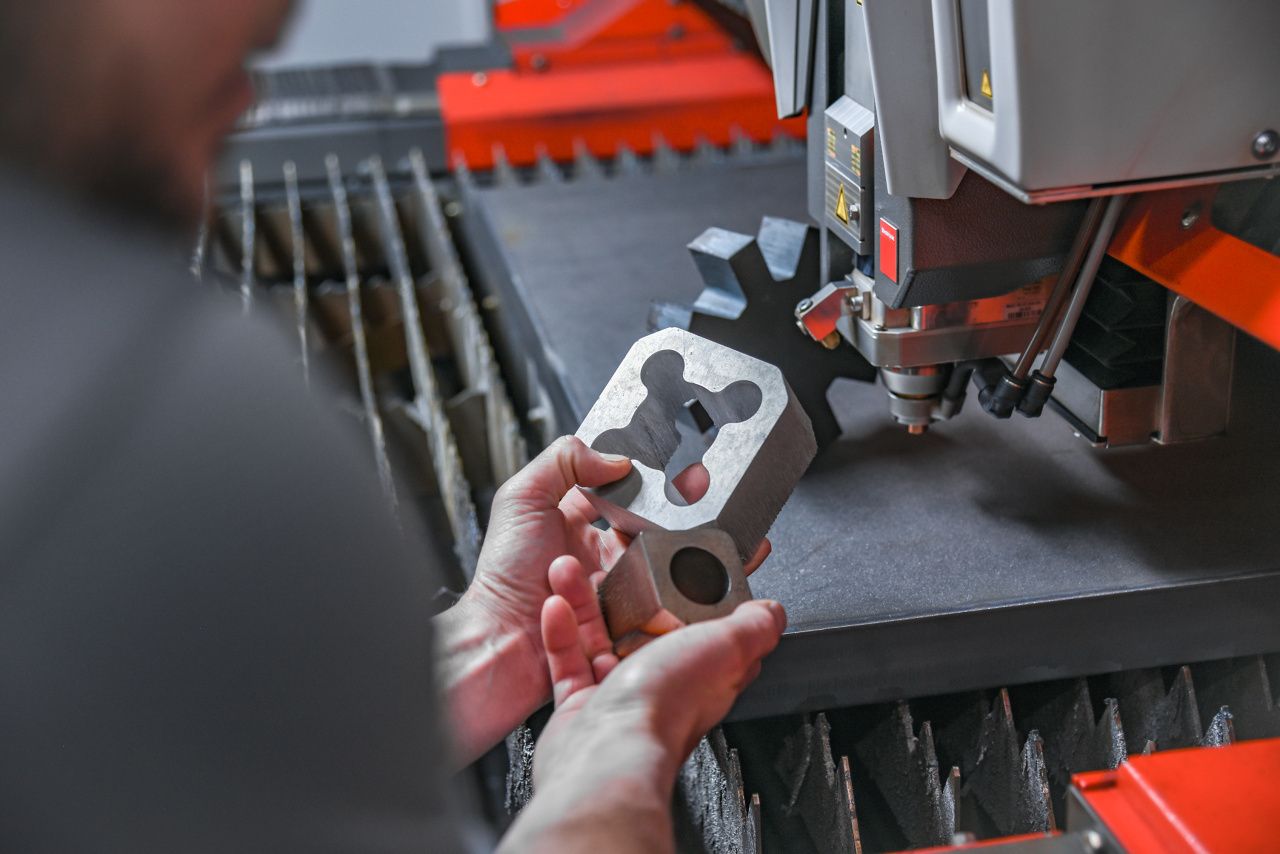
Blog High-Power Fiber Laser Cutting: Pushing Boundaries with New Advancements
Our 30kW Fiber laser cutting machines mark a new era, offering unmatched speed, quality, and versatility. These advancements have made it possible to cut a wide range of materials, from thin sheets to thick plates, with superior efficiency and precision. Fabricators no longer need to maintain older CO2 machines for thick steel cutting—fiber laser technology now addresses this need with cutting-edge solutions.
Overcoming Challenges of Beam Characteristics in Fiber Lasers
Historically, one of the biggest hurdles in using fiber lasers for cutting thick steel was their small beam diameter. While ideal for high-density, nitrogen-assisted cutting, the smaller beam struggled with oxygen-assisted cutting due to the difficulty in expelling large amounts of molten material.
By comparison, CO2 lasers, with their larger beam profiles, excelled in oxygen-assisted cutting of thicker plates. Fiber lasers were typically limited to thin and medium materials, especially in applications demanding high precision.
However, the ability of fiber lasers to achieve high energy density and efficient high-pressure material expulsion makes them excellent for cutting thick stainless steel and aluminum up to 1.5 inches thick with nitrogen assist.
Advancements in Beam Shaping for Thicker Materials
The introduction of BeamShaper technology has revolutionized fiber laser performance for thick steel cutting. This innovation allows fabricators to optimize the beam profile, adapting it for various material thicknesses:
- Standard Beam Profile: Ideal for thin to medium materials, maintaining high energy density for faster, precise cutting.
- Modified Beam Profile (BeamShaper): Designed for oxygen-assisted cutting of thick steel, it broadens the beam profile to create a more suitable energy distribution.
This capability enables faster processing of thick plates, delivering edge quality comparable to CO2 lasers. Coupled with CNC-controlled cutting heads capable of adjusting focal lengths dynamically, BeamShaper technology has made fiber lasers a comprehensive solution for all sheet and plate cutting requirements.
Gas Mixing: A Game-Changer in Assist Gas Technology
Traditionally, laser cutting relied on oxygen, nitrogen, or occasionally dry compressed air as assist gases. Recent breakthroughs have introduced gas mixing, which blends oxygen (up to 6%) into nitrogen for significant benefits:
- Up to 20% faster cutting speeds.
- Increased thickness capacity by up to 25%.
- Reduced edge burr on thick aluminum and stainless steel.
- Enhanced paint adhesion on thick steel by eliminating traditional oxide flaking associated with pure oxygen cutting.
These advantages are most pronounced in high-power fiber lasers above 12kW, where the synergy between power and assist gas mixture significantly improves productivity. Digital gas mixing units ensure precise control, tailoring gas ratios to specific materials and thicknesses for optimal results.
Advanced Cutting Head Technologies: Precision Meets Automation
Modern cutting heads incorporate groundbreaking features designed to enhance precision and autonomy:
- Variable Telescopic Magnification:
• Adjusts focal length and spot size automatically.
• Tailors beam characteristics to material thickness and type. - Automated Nozzle Systems:
• CNC-controlled nozzle changers switch nozzle sizes and types based on cutting requirements.
• Automatic nozzle centering, inspection, and calibration ensure consistent performance. - Kerf Scanning Systems:
• Continuously monitor the cut channel for irregularities.
• Retrace and re-cut any areas where inconsistencies occur.
• Perform automatic nozzle inspections, replacements, and height calibrations if necessary.
These technologies reduce downtime, ensure cut continuity, and minimize errors, making fully autonomous cutting a reality.
Eliminating Variables for Consistent Quality
The complexity of laser cutting introduces numerous variables—focal length, beam profile, gas ratios, and nozzle alignment, to name a few. Advanced fiber laser systems now eliminate these uncertainties through fully automated setups, ensuring consistent:
- Cut quality across varying materials and thicknesses.
- Processing speed to meet tight production schedules.
- Operational reliability with reduced machine wear.
By automating processes like beam shaping, gas mixing, and kerf monitoring, these technologies empower manufacturers to achieve superior results while reducing reliance on skilled operators.
Fiber Lasers for the Future
The latest advancements in high-power fiber laser cutting have redefined the boundaries of manufacturing efficiency. From overcoming the limitations of small beam profiles to enabling high-speed, high-quality cutting with advanced gas mixing and cutting head technologies, fiber lasers now provide a comprehensive solution for fabricators.
With reduced variables, improved automation, and enhanced performance, fabricators can rely on fiber laser technology to meet their sheet and plate cutting needs while staying competitive in an ever-evolving industry. Whether it's precision cutting for thin materials or heavy-duty processing for thick plates, these innovations ensure that fiber lasers remain the cutting-edge choice for modern manufacturing.