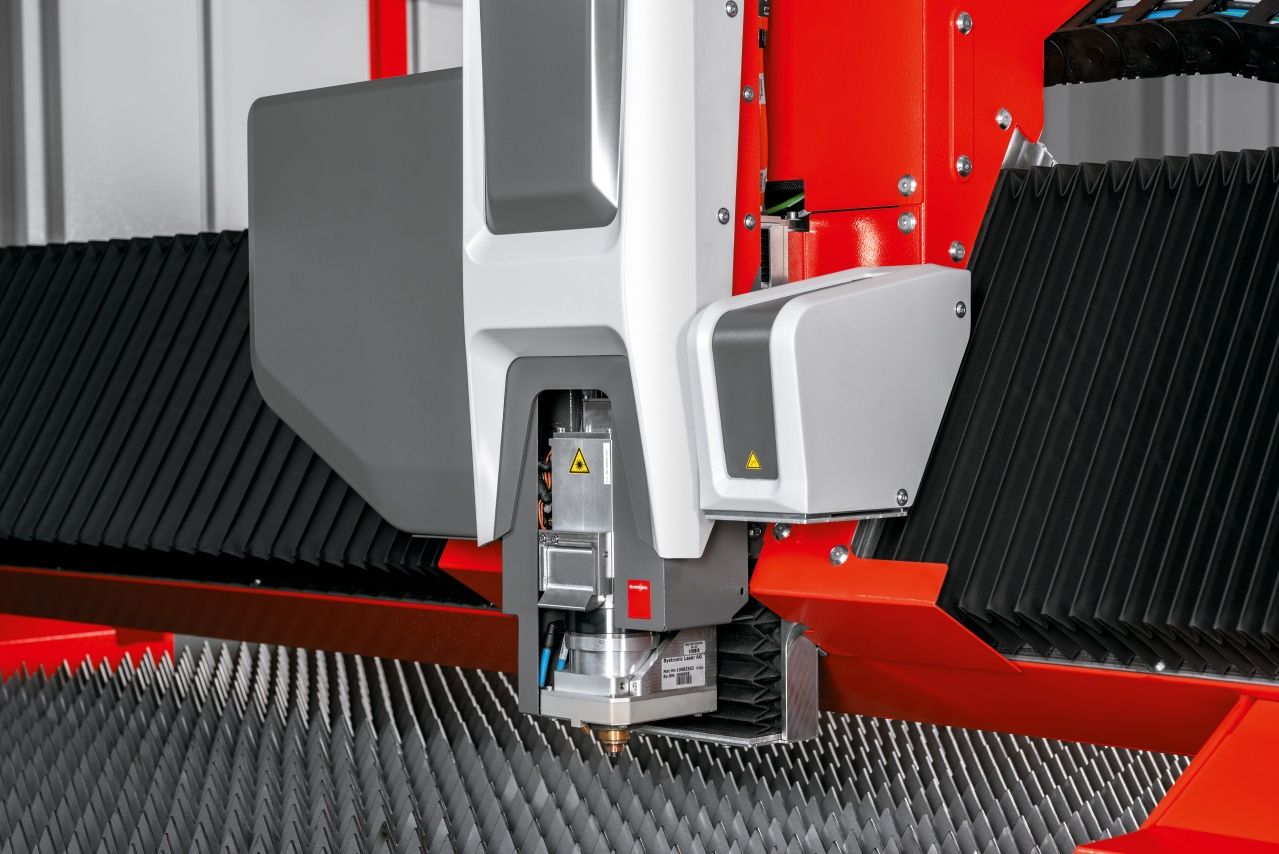
Blog New Fiber Laser Cutting Technologies
Our latest 15kW Fiber laser cutting machines not only represent a leap in cutting speed capabilities but also in cut quality capabilities on thick plate. Many fabricators who cut materials from thin to thick have maintained their older CO2 machines just to cut the thicker steel materials and a Fiber laser machine to cut the thin to medium range of materials. With the latest BeamShaper option, coupled with higher fiber laser powers, this is no longer necessary.
Challenges Posed by Beam Characteristics
One of the biggest challenges of cutting thick plate with oxygen on a Fiber laser has always been the small beam diameter characteristics. After focusing, the small beam became even smaller and so it was difficult to expel large amounts of molten material when utilizing oxygen assist cutting process. For this reason, the larger beam profile created by the CO2 laser was more beneficial for oxygen cutting of thick steel materials. The small Fiber beam profile though was excellent for the nitrogen assist cutting process, due to the high energy density created by the smaller beam profile and the high-pressure expulsion of the molten material. In fact, this process lends itself quite well even with thick plate cutting of stainless and aluminum materials up to 1.500 inches thick cut with Fiber.
Advancements in Beam Shaping
The BeamShaper option effectively bridges the gap between CO2 and Fiber laser capabilities with respect to cutting thicker steel plate with oxygen. For the thin to medium thickness materials, the standard Fiber laser beam characteristics provide the benefits. For thicker steel plate cutting with oxygen, the BeamShaper option effectively adapts the beam to a larger beam profile with a broader distribution of the energy density, creating a better beam profile suitable for oxygen cutting of thick mild steel. The results are faster speeds in thick plate processing with oxygen and edge quality that rivals a CO2 edge. Our latest CNC-controlled cutting head also has the ability to change the effective focal length depending on the material to be cut. This advancement in Fiber laser cutting technology represents a significant leap in capabilities. Fabricators can now rely on one laser technology for all their sheet and plate cutting requirements.
Advanced Cutting Head Technologies
Advanced cutting heads are adapted with variable telescopic magnification which automatically adjusts the focal length and spot size. These cutting heads include automatic CNC-controlled focal positions based on the material to be cut, and nozzle changers have the ability to change the nozzle size and type automatically depending on the material to be cut. With a Kerf Scanning system, an optical cut monitor is constantly monitoring the cut channel (kerf) for irregularities in visible light emitting from the cut zone. In the case where an irregularity is detected, the system will retrace to just prior to where the irregularity occurred and cut again through the existing channel to ensure the proper cut has been re-established. If it cannot re-establish the cut, the laser cutting system will then perform a nozzle centering and optical inspection of the nozzle, and if needed replace the nozzle and calibrate the height. The cutting head then returns to where it first encountered the irregularity and re-establishes the cut and continues to monitor the cut channel throughout the cutting process.
Automating for Consistency, Quality, and Throughput
With advanced cutting head technologies, setups for focal length, spot size, beam shaping, nozzle selection, nozzle centering, nozzle inspection, and calibration, greatly increases the quality and consistency of cutting and also eliminate variables during the process. All of these advanced cutting technologies combined with material automation make it possible to operate unmanned laser cutting systems in the off-shifts and over weekends, and with consistently high-quality results and high throughput capabilities.