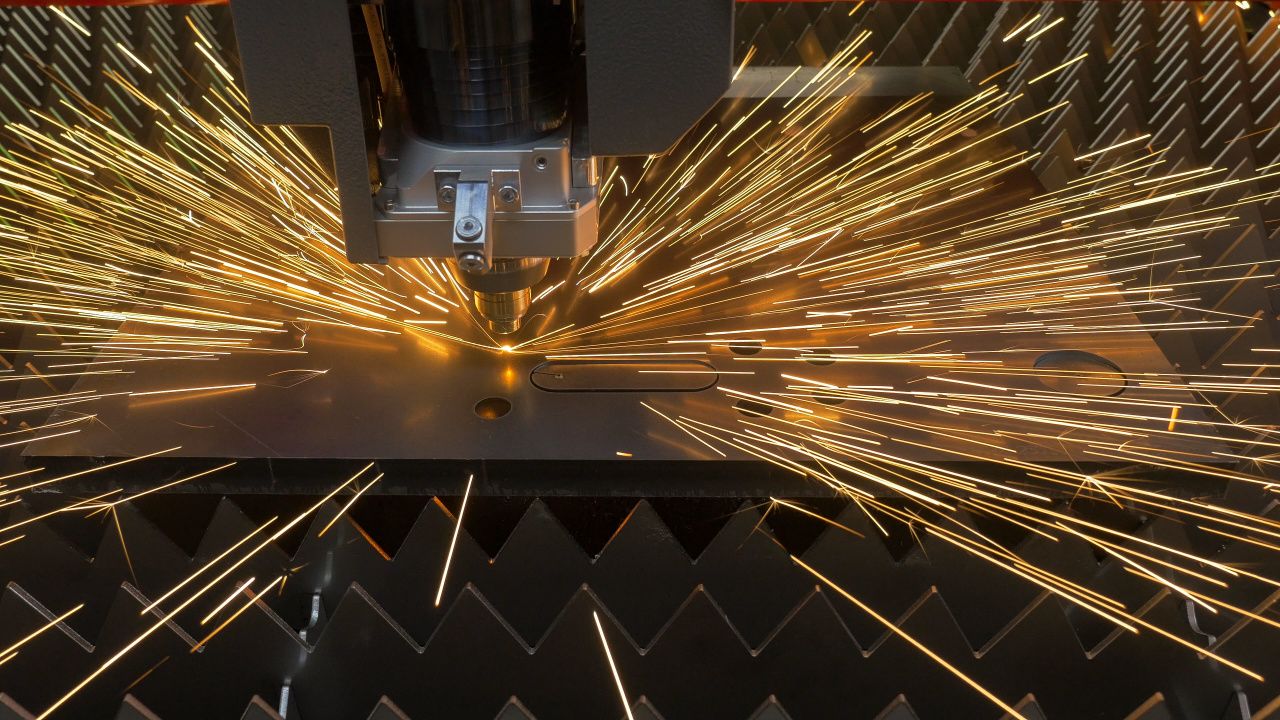
Blog CO2 vs Fiber Lasers: Evaluating the Cost Differences
When looking at Fiber laser cutting technology and considering the productivity benefits, which include less than half the operating costs and more than double the speed when compared to CO2 lasers, it is obvious why Fiber lasers have become so popular.
Technology contributions to operating cost
The focused beam of even a 2kW Fiber laser possesses 5 times more power density and 2.5 times more absorption than a 4kW CO2-focused beam due to the nature of the beam size and the wavelength comparison. What this means is that higher feed rates can be achieved with a Fiber laser as compared to a CO2 laser, producing up to five times more parts per unit of time depending on the Fiber laser power. Because you can produce three to five times more parts with Fiber lasers, you have reduced the time to produce the parts and effectively reduced the cost per part. By producing parts faster, you have created additional machine capacity to cut additional parts, increasing revenue.
Electrical consumption on a Fiber laser is lower by almost three times as compared to a CO2 laser of the same output power wattage, lowering your effective cost per part. Eliminating maintenance on beam delivery optics, the beam path bellows and purge system, and the vacuum pump, frees up additional machine capacity.
Not having to wait 10 minutes until the CO2 laser is at full operating potential on a daily basis is another capacity opportunity gained. The fact that the beam alignment and the beam size never change on the Fiber laser facilitates consistency of cut and repeatability of parameters on a daily basis. This benefit increases machine capacity by not spending time adjusting the parameters because the parts are always consistent in cut quality from shift to shift and from day to day.
Fixed and variable cost comparisons
While we sometimes become attached to our equipment, the answer as to when equipment needs to be replaced should be an objective one rather than a subjective one. Each company is slightly different in how they approach their fixed and variable costs and what they consider to be an effective return on investment (ROI) for considering new equipment. However, there is commonality when it comes to analyzing the cost per part. No matter how fixed costs and variable costs are calculated, all related fixed and variable costs eventually affect the cost per part, and ultimately a company’s competitiveness.
Repair and maintenance cost comparisons
One of the largest variable cost factors for older equipment is the cost to repair and maintain it. How much is the cost to repair the equipment contributing to the total variable cost? How much more, as a percentage, does the cost to repair and maintain differ from when the machine was new? Of course, you will need to make this comparison based on an equal number of operating hours.
To see true costs and trends, costs will need to be evaluated on a rolling basis and over time. Was it a one-time large repair cost or does the trend show increasing repair costs over time? Remember to include lost machine revenue due to downtime with the machine repair costs. Excessive repair costs significantly affect your profit and your cost per part.
Actual ‘cost per part’ factors
What about the actual ‘cost per part’ on your current equipment vs comparing the production of that same part on a new Fiber laser machine? If we compare the new cost per part calculation based on the costs (fixed and variable) and the run time estimates from the fiber, how much lower in percentage is the cost per part compared to the current equipment? Both the trend line in cost per part and lost bids should be analyzed to determine when these increasing trends become a trigger for considering new equipment. Lost bids and a higher cost per part affect sales revenues and profits.
Justifying the Fiber laser investment
After evaluating the full potential of Fiber laser technology, you will realize that you can produce three to five times more parts at half the operating costs, while simultaneously creating more machine capacity. This will enable you to cut additional parts and win more competitive bids thanks to a lower overall cost per part.