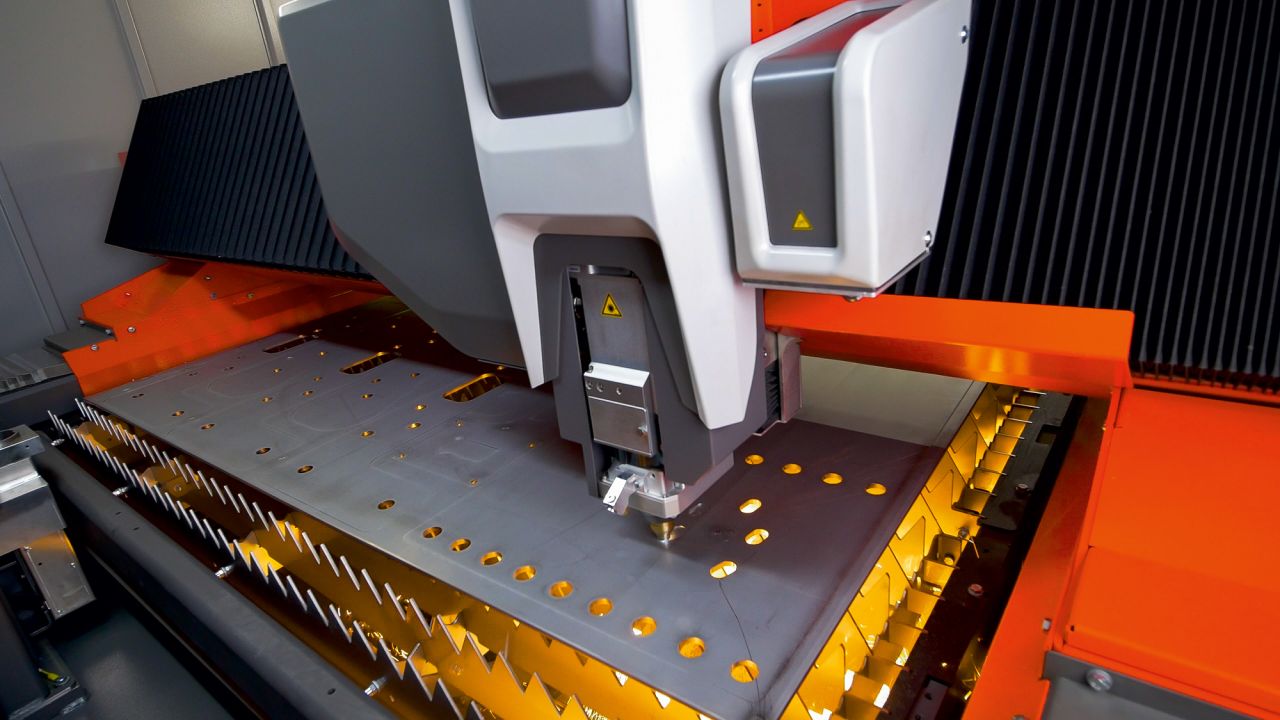
Blog Automating Sheet Metal Fabrication from End-to-End
At the center of the capacity demand is the high-power fiber laser that creates a “pull demand” from front-end business, engineering, and material logistics and a “push demand” to downstream machines and their processes.
At the front end, we have the pull demand requirement to process incoming orders more efficiently through the ERP system generating the bill of materials (BOM); material requirements planning (MRP); and with a manufacturing execution system (MES), processing, routing, programming, and scheduling. This is a 'must' if you expect to maintain the pace with the volume of production that a high-power fiber laser cutter produces.
Scheduling with MES
After a bid is won, the parts already in the ERP are activated for production. Materials are prepared and machine programs are generated by the Manufacturing Execution System (MES) in conjunction with a CAD/CAM system. MES will also schedule the job based on the process and machine routings. Because MES operates in real time, any process delays or advancements affect the delivery date in real time. The MES also evaluates the machine availability and the part status in real time and makes scheduling adjustments to all other parts requiring the same processes and machines. The same holds true for hot jobs that are introduced into the MES system. In the case of a hot job that needs to be processed immediately, the MES adapts all other jobs and generates new completion dates based on the process times and machines utilized by introducing the hot job.
Eliminating Manual Machine Setups
In the past, laser-cutting operators had to make several manual adjustments to the machine before each material was cut. This would involve adapting the appropriate cutting parameters, setting the proper focal lengths and focal positions, selecting the correct nozzle types, and centering the nozzle. While the machine was running, the operator would be required to monitor cut conditions as even an incidental bump to the nozzle could affect the nozzle centering, posing a significant risk during unmanned operations. When this occurred, the operator would need to stop production, inspect the nozzle for damage, replace the nozzle if necessary, and then re-center the nozzle. Today, new fiber laser cutting machine automation technologies address these concerns and they require little to no supervision.
- Fixed cutting heads now feature automatic focal positions based on the material to be cut, and variable telescopic magnification automatically adjusts the focal length and the respective spot size.
- Nozzle centering and calibration are carried out automatically. Depending on the material to be cut, Nozzle Changers can change the nozzle size and type automatically.
- Automation technologies for monitoring nozzle centering, nozzle calibrations, and cut kerf, greatly enhance a machine’s ability to run in off-shifts and weekend shifts without the inherent risks associated with unattended operations.
With these advancements, and automated material handling and storage systems, fiber laser cutting systems can now operate fully automatically.
Material Logistics
The next logistics step in the 'capacity demands' cycle lies in the storage and timely delivery of the materials to the machine for processing. Once at the machine, the material handling automation system can load the raw materials. This represents the final step of the “pull demand” from the fiber laser cutter.
Parts sorting and unloading follow. This represents the start of the “push demand” cycle. After cutting, the automated part sorting system sorts the cut parts onto skids and stacks them by the customer, job assembly, or next machine process. This is the most efficient way to prepare parts for downstream processing.
Downstream Processes
Maintaining a consistent flow of parts to downstream stations is critical for utilizing available machine capacity and not bottlenecking production with an overwhelming “all-at-once” delivery of parts from the laser.
As a press brake operator or weld cell operator, you are aware of the “push demands” that can be produced by even a single high-power fiber laser cutting system. Once at the bending and welding stations, not only can automated bending cells be employed but also automated robotic or cobot-assisted welding systems. As most automated fiber laser cutting systems run multiple shifts so must the downstream machines. The beauty of these robotic systems is that they can run in multiple shifts and on weekends with little to no supervision. Part movements can be automated by autonomous guided vehicles (AGVs) that basically move part skids from laser cutting to bending, to welding and paint stations without forklift material movers.
End-to-End Efficiency
From the moment an order is received until it ships, the entire fabrication process needs to be streamlined and automated. Emphasizing the importance of automating front-end business software systems, material automation, sorting, automated bending, and welding cells, will satisfy both the pull demand and push demand of high-power fiber lasers and provide for an efficient end-to-end sheet metal fabrication process.