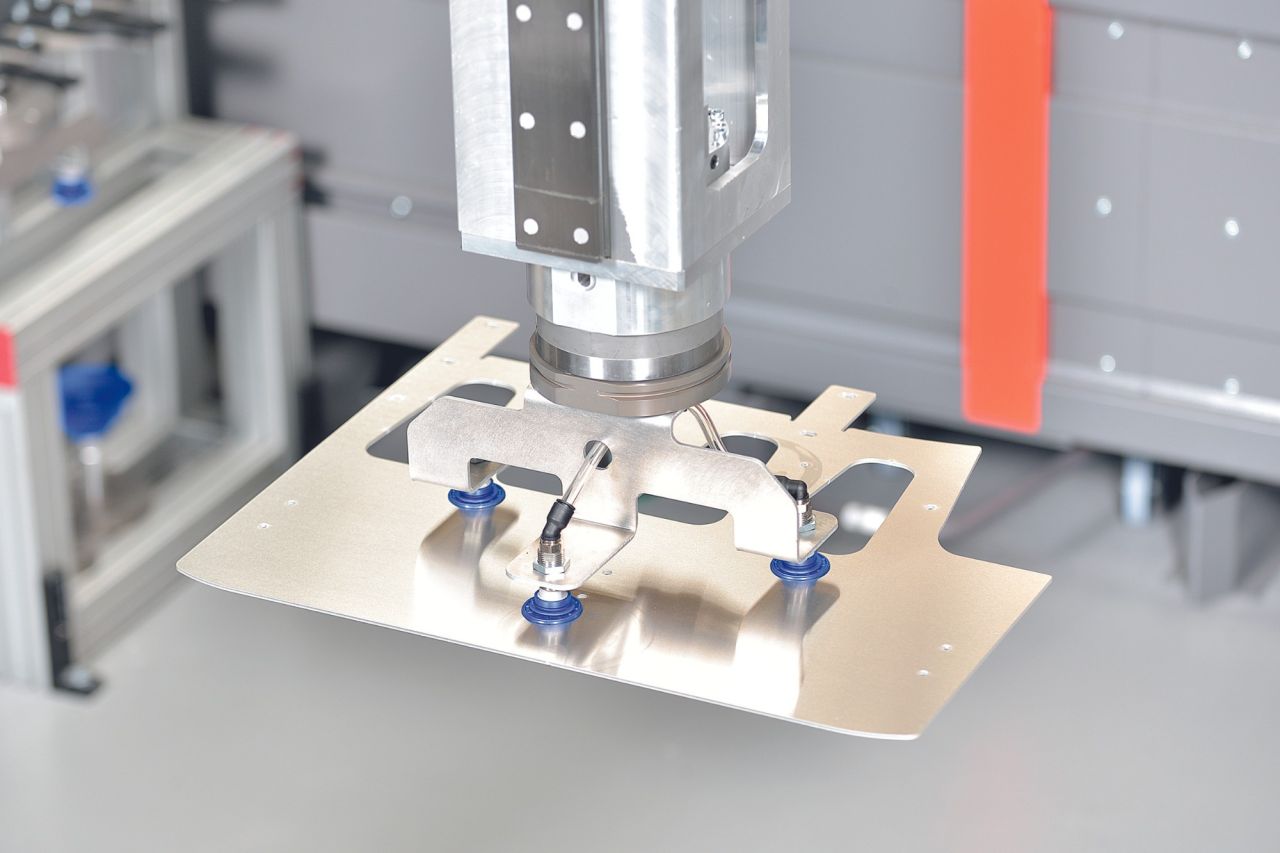
Blog Analyzing the Metal Fabricating Value Chain (Part 2)
For the most part, laser cutting systems without material handling automation display the most variability in their production time during the loading and unloading process. If you analyze the waiting or idle times from the machine data, the waiting times are notoriously evident. This is due to either a lack of raw materials having been supplied to the machine or a lack of unloading cut parts before the machine has finished processing the previous sheet. Herein lie the additional opportunities for improving material handling as a way to increase manufacturing efficiency and reduce overall processing time.
Supplying raw materials
So the programming system has released the cut programs to the machine. How does your system react to this request? Does someone now retrieve the raw material from a material storage area using a forklift and bring it to the machine? How much time is accumulated performing this action for each and every material changeover? If you are in a high-mix environment with many daily changeovers, an automated material storage system can supply multiple materials types and thicknesses across multiple machines. With an automated material storage system, as programs are released to the laser cutting machines and loaded for processing, the communications to the material storage system are achieved automatically. Once the first order of material is delivered to the laser cutter, the subsequent material order can already be delivered during the processing of the last sheet of the first order. This way, the raw material is moving to the machine while the machine is still processing.
Automating the load process
Once the laser cutting machine is presented with the raw material stack, the next step is to automate the raw material loading. If automated, the loading of the material becomes part of the automatic sequencing tied to the machine’s request for material. No more waiting from sheet to sheet and from order to order. Sheets are loaded onto the secondary shuttle table while the laser cutter is cutting on the primary table. But there is yet another important sequence that must occur in between the raw materials being loaded. If the cut material is not unloaded in a timely manner then waiting times will accumulate.
Automating the unload process
Automating the unloading process is extremely critical as all other processes of loading and cutting are dependently tied to this very important sequence. A bottleneck is created without the unloading taking place in a timely manner. At this point, there are two ways to address the unload automation process. One method is to unload the entire cut sheet with parts using an unload fork system. Another, and more efficient method, is to already have the parts unloaded using an automated sorting system for the parts and a fork system to remove the material skeleton when completed. The automated sorting system sorts parts from the sheet based on the order it belongs to. It also organizes ‘like’ parts in a neet stack for the next process. This greatly reduces process times in sorting the parts manually from the cut sheet and reduces errors in stacking similar part revisions
Reducing the bottlenecks
We have now analyzed one of the most common areas for process variability and bottlenecks in the fabricating value chain due to unplanned waiting times. If this variability exists, it is probably not being accounted for in job quotes, and more than likely affecting your promised customer delivery dates.
In part 3 of ‘Analyzing the Metal Fabricating Value Chain,’ we will look at analyzing the bending opportunities as the next sequence in the value chain. Here too are additional opportunities to reduce non-productive waiting times and increase efficiencies in your metal fabrication value chain. Continuous improvement and continuous innovation are how leading-edge companies continue to grow and expand. It’s not about how the process is today but the vision of how it could be, given advancements in technology.