How AI reduces machine downtimes
Making metal processing more efficient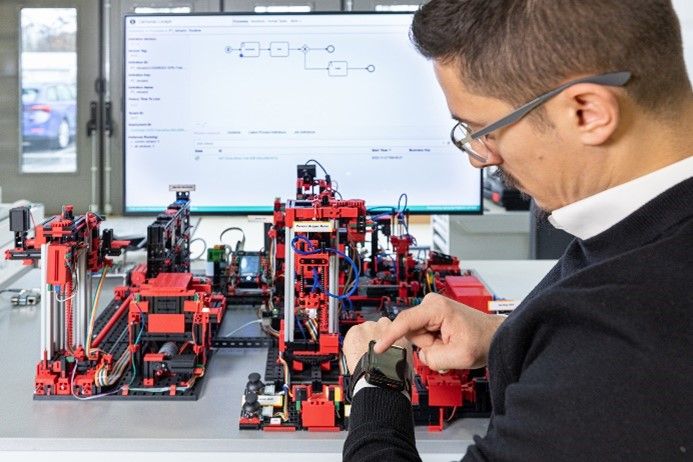
AI makes metal processing more efficient: It quickly detects quality defects in welding seams and can instruct employees on how to rectify faults.
If a fault occurs unnoticed on a machine, it produces rejects until someone notices the quality defects. The machine is at a standstill until the source of the fault has been found and rectified. Such downtimes must be avoided, as they cost companies dearly. A research team from the Fraunhofer Institute for Manufacturing Engineering and Automation IPA, together with two industrial partners, has developed a method for using artificial intelligence to reduce these costly production interruptions.
The project focuses on ultrasonic welding. An AI monitors the process in three ways: it evaluates camera images of the weld seams in real time, measures the power consumption, which increases with the wear and tear of wearing parts, and checks the thickness of the welded pipes. As soon as the AI detects a poor weld seam, a message appears on the smart watch of the machine operator responsible. It is linked to a recommendation for action so that the fault can be rectified as quickly as possible and without unsystematic trial and error.
The application is still a demonstrator. However, the developers and industry partners are confident that the tool could shorten the duration of machine downtimes by up to 20 percent and reduce the reject rate by around 0.5 percent once it has been rolled out. In addition, the costs for maintenance and repair work are expected to fall.