Steel production with electricity
Making the industry cleaner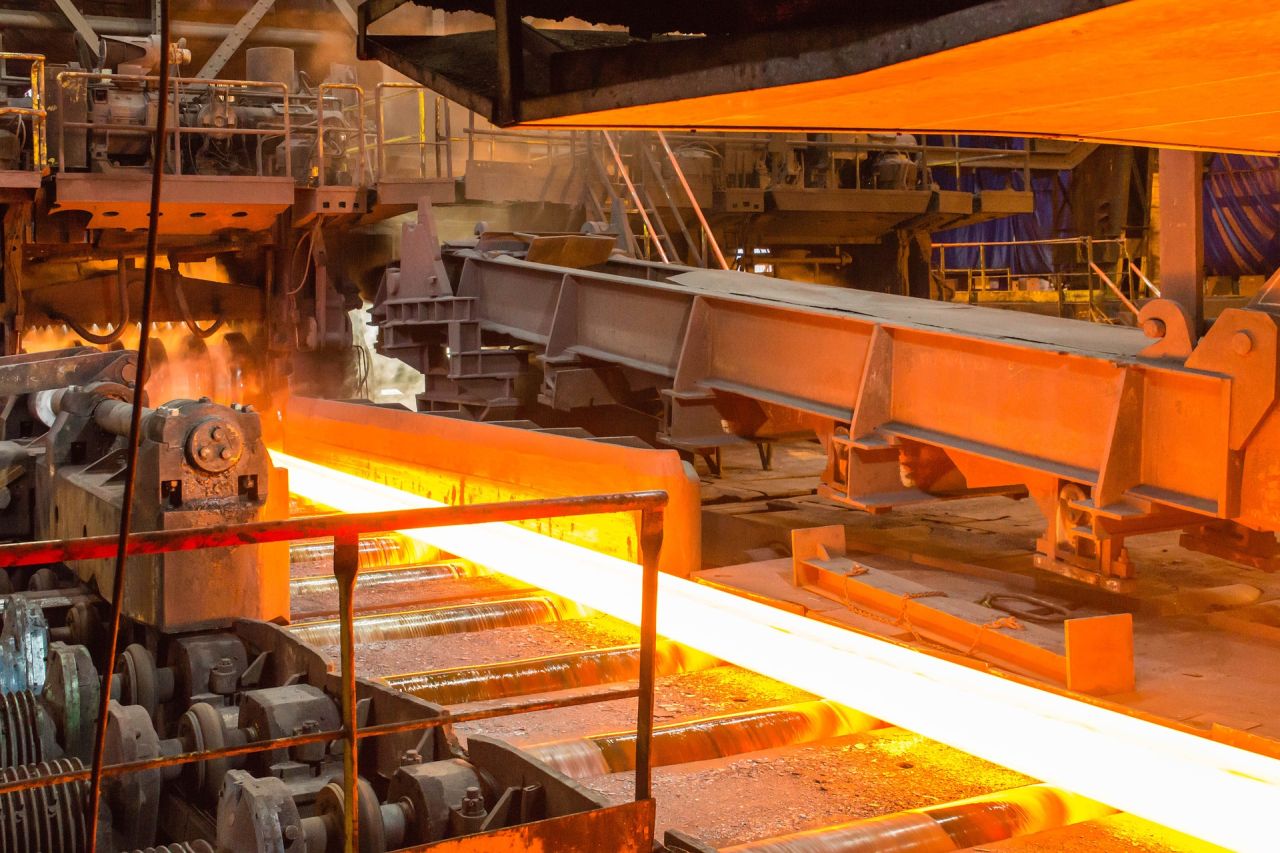
An MIT spin-off wants to make steel production greener. With a method that is already helping mining companies to recover high-quality metals.
Steel production is responsible for around 7 to 9 percent of global greenhouse gas emissions. Boston Metal, a spin-off from the Massachusetts Institute of Technology (MIT), is now trying to make the industry cleaner with an electrochemical process. This would make many steps in steel production superfluous; oxygen would be the only by-product released.
Molten oxide electrolysis (MOE) takes place in modular cells, each the size of a school bus. The iron ore rock is placed in the cell, which contains a cathode (the negative pole of the MOE cell) and an inert anode immersed in a liquid electrolyte. When the current flows between the anode and cathode and the cell reaches a temperature of around 1600 degrees Celsius, the iron oxide bonds in the ore are split. Pure liquid metal collects at the bottom, which can be tapped off. The process does not require water, hazardous chemicals or precious metal catalysts.
Boston Metal is already using MOE to help mining companies recover high-grade metals from their mining waste, which normally requires costly treatment or storage. The process could later be used for the production of many other metals. Boston Metal expects its method for decarbonizing steel to reach commercial scale by 2026.