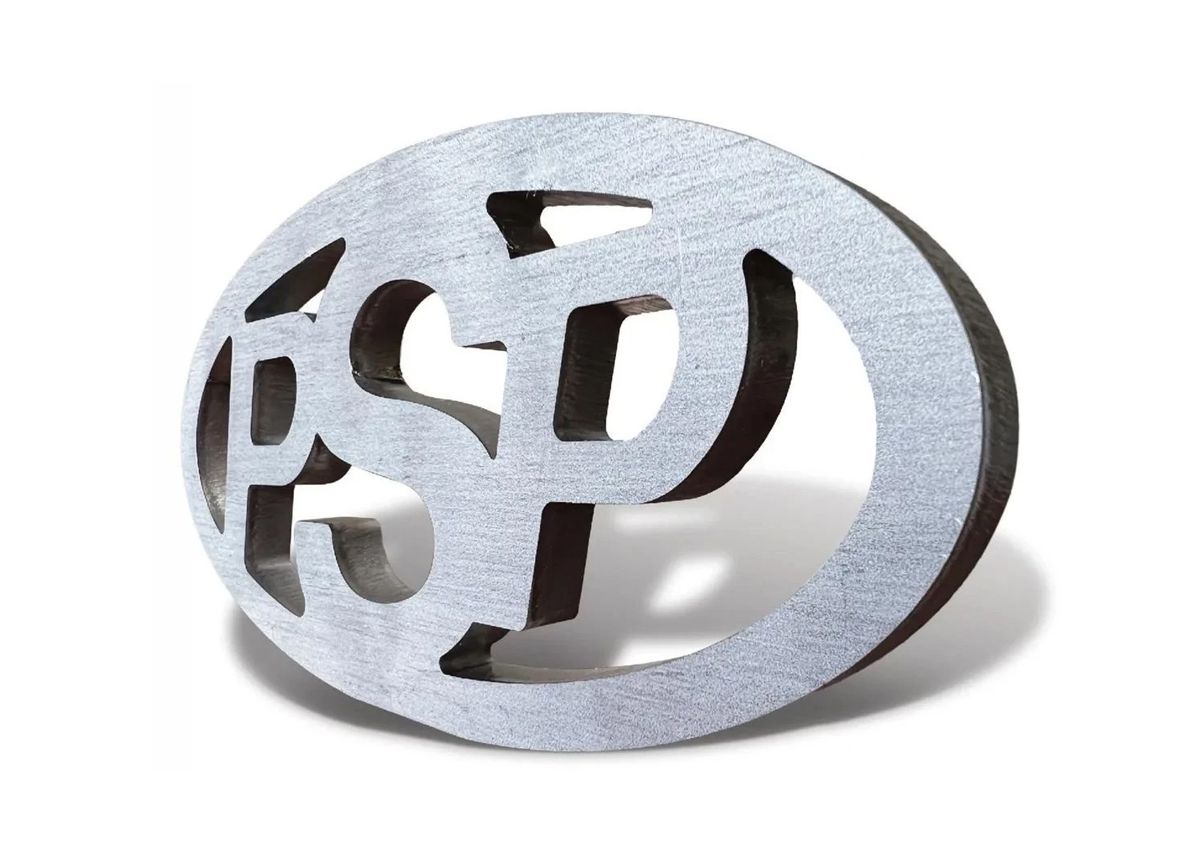
News POWERHOUSE: Penn Stainless Products
Service center implements fiber laser cutting for thick materials
Quakertown, Pennsylvania-based Penn Stainless Products Inc. has a team of processing experts, who lean on years of experience cutting parts. The company originally was a fabrication business that began focusing on distribution and processing in 1979. Today, it’s a full-line service center with 220,000 square feet at its main facility and an additional 35,000 square feet in Jackson Center, Pennsylvania.
The company specializes in custom, challenging requirements. It stocks a wide selection of plate and sheet inventory so customers can select the most cost-effective material and process over 30 grades, including 300 and 400 series stainless, duplex steels, 17-4PH and high-temperature grades, as well as large sizes.
“We engage in a consultative process with our customers since we offer plasma, laser and waterjet cutting,” says Jason Martineau, director of sales and marketing. “Cost and total value need to be balanced and communicated to the customer so they can make the best selection for their application and needs.”
In some instances – say, on a 1-inch-thick plate flange with bolt holes – laser will work just fine, he says. “It’s lower cost than waterjet cutting and offers a similar tolerance. However, if the customer is working on something like a vacuum chamber application, they may insist on no heat-effect zone, which the laser is unable to accomplish.”
Large Capacity
Penn Stainless has switched over to Hoffman Estates, Illinois-based Bystronic’s ByStar Fiber Lasers for all in-house stainless steel plate and sheet laser processing. ByStar Fiber lasers are versatile, cutting everything from stainless steel steel to aluminum and non-ferrous materials up to 2 inches thick. Penn Stainless is taking full advantage of that capability with cutting beds that can accommodate stainless steel sheet and plate up to 98 inches by 240 inches.
"We operated a large-format CO2, laser for about a decade prior to purchasing the ByStar lasers," says Martineau. Penn Stainless now runs three ByStars, two 20 kW and one 15 kW. "The first was ordered for our Jackson Center location that services western Pennsylvania and the Midwest. We added two lasers in Quakertown about a year later."
Advancements have been made in laser-cutting technology over time to resolve inconsistent beam delivery, excessive heat in the cut material and other limitations, including improved motion systems, better piercing technology and computer controlled software that can direct the output of the laser beam. In addition, "fiber lasers have an advantage over traditional CO2, in that they allow customers to cut reflective materials much better than CO2, lasers ever did," claims Justin Oslosky, direct sales engineer for Bystronic. The ByStar platform provides our highest level of power, which allows users to cut much thicker material."
Today's plate laser cutting machines are designed to be powerful and are optimized to manage larger and thicker materials. At Penn Stainless, the expanded range of capabilities means customers can obtain the quality and cost benefits of laser cutting for much thicker stainless steel plate than would be possible with sheet lasers, including sizes that are outside the range of a typical waterjet cutter.
ByStar fiber lasers also feature a nozzle control tool (NCT) that centers the nozzle quickly and monitors its condition, while KerfScan monitors the cutting process. BeamShaper significantly improves the cut quality on thick materials even when the material is of lesser quality, and ByPos Fiber automatically sets the focus position.
According to Martineau, the lasers' expanded thickness cutting capacity with faster cut speeds compared to waterjet cutting "is a big plus and helps balance workloads across equipment. Moreover, by bringing in three machines, we have built-in redundant capacity and reduced lead times to our customers."
Bright Future
Oslosky says that, of course, there is training required with any new machine but "with fiber technology, the learning curve is significantly less than with CO2. The technology itself, along with our machine controls and software help make it easier for operators and companies."
The ByStar Fiber lasers also feature intuitive user guidance to find cutting parameters for new materials that are unknown. Parameter Wizard will determine the perfect parameters for any material in a matter of minutes, minimizing the time lost with finding new parameters. And operating the touch-screen controls and associated automation is as easy as using a smartphone.
"In the past, CO2 technology leveled out at 6,000 watts and 1-inch-thick material," says Oslosky. "With fiber technology, we now have customers able to cut with 30,000 watts and over 2 inches thick. The technology has come a long way in the last dozen years."
In addition, he points out that fiber laser significantly reduces operating cost and electrical consumption. A good starting point for metals executives who are interested in fiber is to complete a time study to see how it fares compared to their current cutting technology. "The ability to see thicker materials that could only be cut previously with a slower process like a waterjet being cut much faster with fiber can help with their decision-making process."
By Lauren Duensing, Contributing Editor
As published in Modern Metals Magazine, August 2024
Penn Stainless Products