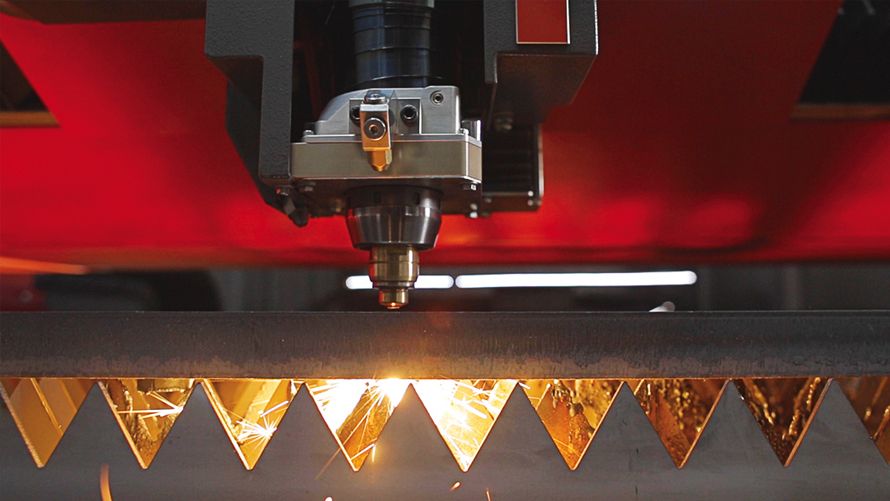
News High-powered lasers and the evolution of assist gases
The emergence of fiber lasers 20kW and higher is forcing fabricators to think differently about how they approach laser cutting.
The increasing adoption rate of high-powered lasers is not likely to end anytime soon. With laser cutting power reaching 20kW, these devices are capable of cutting materials up to 1.5 in. with precision, a thickness once reserved for waterjets and plasma cutting machines.
Adopting these high-powered devices comes with new considerations, however. All metal fabricators love the increased cutting capacity. For example, on average, a new 20-kW fiber laser can increase cutting speeds by up to 50% when compared to a 10-kW fiber laser power source. That comparison is valid when the cutting is done using nitrogen as the laser assist gas, and that’s important to note because nitrogen gas consumption rises dramatically with these new high-powered fiber laser cutting machines.
Legacy equipment simply can’t match the range of material thicknesses that can be cut efficiently with nitrogen on high-powered fiber laser cutting machines. Nitrogen is the gas of choice because it prevents the laser-cut edge from becoming oxidized, which is what happens when oxygen is used as the assist gas. (Powder coatings and paint often cannot adhere to oxidized metal edges.)
That leads to the following scenario: A metal fabricator loves producing more parts per hour than it ever could on its older laser cutting machine, and to minimize downstream handling, such as grinding the edges to remove evidence of oxidation, it uses nitrogen as the assist gas. As a result, the fabricator likely is going to use more nitrogen—especially if it is cutting plate—than it ever did before.
Does the shop seek out larger bulk tanks? That’s a possibility, but it might not be the most cost-effective answer. Relationships with gas suppliers require contracts, which lock metal fabricating companies into a financial arrangement that offers little flexibility. Also, in many instances, the farther away a fab operation is from the gas supplier, the more expensive the gas is.
Increased consumption of nitrogen also begs the question if a facility’s piping system can accommodate the new volume of gas. Re-piping the entire infrastructure might be required with the upsizing of bulk tanks.
After having invested in a new high-powered laser cutting machine including material handling and parts sorting automation, any metal fabricator would show interest in trying to minimize the ongoing costs of running the laser. That’s why more of them are showing an interest in nitrogen generators as part of the equipment mix when they embrace high-powered laser cutting.
Status Report: Nitrogen Generation
Nitrogen generation isn’t new to the metal fabricating sector, but it is being more widely embraced. Many shops might have been suspicious of the technology at one time and found traditional bulk containers or dewars more reliable. Today the high-powered fiber laser’s thirst for nitrogen is changing any lingering doubts into full-fledged interest.
Nitrogen-generation devices don’t really create nitrogen but extract it from the surrounding atmosphere. Nitrogen makes up approximately 78% of the air humans breathe, and oxygen accounts for about 21%. The rest is argon and traces of other gases like carbon dioxide and methane.
There are essentially two methods of generating high-purity nitrogen: membranes and pressure swing adsorption. In the membrane process, gas flows through a collection of hollow fibers; the oxygen molecules flow through because they are smaller than the fibers’ pores, and nitrogen molecules, which are larger than the pores, migrate to the laser (see Fig. 1).
Pressure swing adsorption involves a two-tank setup with a carbon molecular sieve on both tanks to trap oxygen molecules. As one tank is trapping the oxygen, the sieve allows the nitrogen molecules to pass vertically to the second tank. When the first tank can no longer adsorb additional oxygen molecules, a pressure swing occurs between the two tanks, with the second tank becoming pressurized and the first tank expelling its collection of oxygen. The first tank then is filled with nitrogen, and the separation cycle begins again. The entire process is in a constant state of balance (see Fig. 2).
Currently, the pressure swing adsorption approach is the most common for nitrogen generation for laser cutting. It can produce a very pure nitrogen gas and deliver strong flow rates at higher pressures for those laser cutting machines that require them.
Enter the Gas Mix
In recent years a lot of research has been conducted with gas mixing—adding another gas to nitrogen during the laser cutting process. The primary motivation was increased cutting rates; the idea was that the presence of some oxygen could elevate the cutting temperatures, thereby removing metal at a higher rate. This worked in many instances, but not in all cases.
A recently discovered benefit of gas mixing is the ability to reduce the fiber burr—that burr and dross on the bottom side of metal, particularly aluminum, which appears after the metal is cut with any high-powered fiber laser using an inert gas such as nitrogen. This burr results from the material cooling too fast as it is ejected through the bottom surface and recast on the edges of the profile. The presence of oxygen in the gas mix and the resultant increase in cut temperature helps to minimize the burr to the point that many metal fabricators can live with the laser-cut results and not worry about downstream deburring.
The results of using this type of gas mix can be pretty dramatic when compared to using straight nitrogen. For instance, a test involving a 6-kW fiber laser cutting 0.375-in. mild steel revealed that a gas mix of 97% nitrogen and 3% oxygen produced a cutting speed of 110 IPM, which was a marked improvement over the 90 IPM using only nitrogen as the assist gas.
The results get more dramatic with higher-powered machines. A 10-kW fiber laser processing the same material and using the same gas mixture achieved cutting speeds as high as 230 IPM. Using straight nitrogen as the laser assist gas, the same machine reached only 183 IPM.
Those are just two examples, but metal fabricators can expect higher-quality edges, increased cutting speeds, and reduced nitrogen consumption when using these gas mixes. Obviously, the results will differ depending on the laser cutting machine being used and the prescribed gas ratio mixtures.
Metal fabricators worried about oxidation of edges when using a gas mix with oxygen have every right to be concerned, but they also might be surprised. Some metal manufacturers have found that parts cut with a gas mixture of 95% nitrogen and 5% oxygen accepted a paint coating well enough and performed satisfactorily in scratch-resistance and weather tests. On the other hand, some manufacturing companies that required parts to stand up to extensive salt spray testing, where parts are blasted with salt and water over a long period of time, discovered that using the gas mix during laser cutting opened the door to more test failures. Again, the application and user expectations drive whether the use of this gas mix makes sense.
These gas mixes are delivered to the laser cutting machine through an on-demand gas-mixing system, which is both small in size and inexpensive. The gas mixer makes it easy to dial in the correct ratio of nitrogen and oxygen for the cutting application.
These gas mixers are connected to the nitrogen-generation system and typically high-pressure dewars of oxygen. A bulk supply of oxygen typically doesn’t work for this setup because the feed pressure is too low. The feed pressure from one of these oxygen tanks might be 145 PSI, which is inadequate when compared to the feed pressure of 350 PSI from the nitrogen-generation system. If the incoming oxygen feed pressure is 20 PSI less than the nitrogen feed pressure, the nitrogen will displace the oxygen, and the gas flow will become unbalanced. The high-pressure dewars of oxygen keep that gas mixture in the correct balance.
The overall size of the nitrogen-generation system comprises two main parts: the generation unit and the storage tanks. The generation unit takes up about 6 by 6 sq. ft. and stands about 8 ft. tall. The storage tanks, which look like a stack of scuba tanks, are stacked close to the generation unit, adding a few feet to the overall footprint. The on-demand gas mixer is small by comparison: 2 by 2.5 ft. and about 3 ft. tall.
The size of the nitrogen-generation equipment makes it a good candidate for placing it above the laser cutting machine, say in a mezzanine. To make the most of their existing square footage, shops are looking to go vertical wherever they can with ancillary support equipment for their workhorse machine tools. A nitrogen-generation system is a suitable candidate for this approach.
Moving Forward
Research on gas mixing is likely to continue as laser cutting machines grow in power and metal fabricators open their minds to what is possible beyond using pure nitrogen as an assist gas. Machine tool companies will explore just how much oxygen they might be able to introduce for a cutting application that boosts cutting speed and improves cut edges without leaving too much evidence of oxidation. These companies also will take a look at alternative gases to add to the mix, especially given the increased amount of titanium and other specialty metals that fabricators are being asked to cut for the growing commercial space industry.
Despite all the positives associated with nitrogen generation and the new gas mixes that are available with these systems, some metal fabricators are still dragging their feet. The initial capital investment can be a turnoff, particularly if their current gas delivery method and storage tanks work.
That’s where these company owners and managers need to change their perspective. Nitrogen generation represents a chance for metal fabricators to improve production rates, achieve cost certainty, and even boost product quality, with the potential to see further improvements thanks to continuing industry research. It’s getting to the point where fabricators can’t afford to ignore nitrogen generation if they are running high-powered laser cutting machines.
By: Dan Cortez, Applications Manager for Bystronic Inc.
As published in The Fabricator magazine