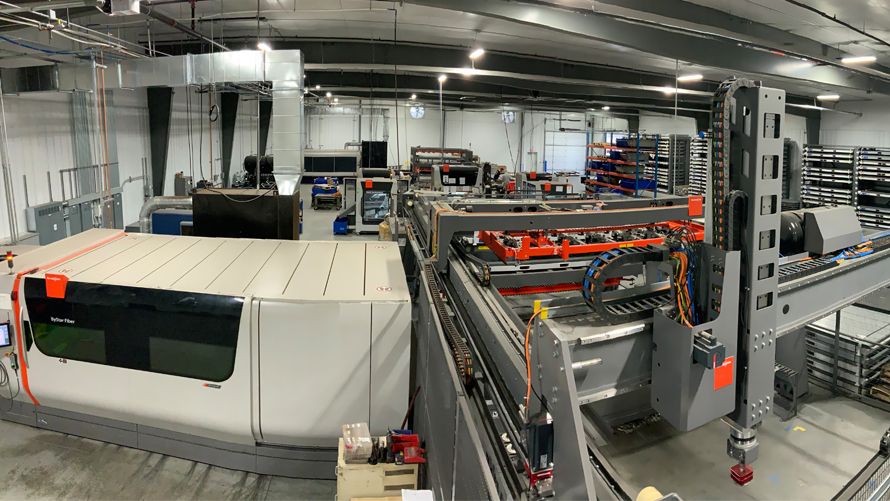
News High power fiber laser cutting: Doing more with less
In a growing, yet competitive market, companies are looking to do more with less-that is, more throughput with less labor, less space, and less overhead.
Located in the city limits of Lincoln, Nebraska is Kinney Manufacturing (intometal.com), a contract manufacturer with extensive capabilities in engineering, fabrication, finishing, machining, quality, and welding. The company has been investing in high-power fiber lasers and automated solutions to drive increased throughput, efficiency, and profitability.
When traveling to Lincoln, one notices how this company is completely surrounded by vast acres of farmland and wide-open prairies, and because of this, how this contributes to how competitive the local labor market can be. This factor that has led Kinney Manufacturing to be able to do more with less. Today, companies like Kinney Manufacturing are leveraging high-powered lasers and material automation to create a winning combination. The company uses a 10 kW fiber laser cutting system with a fully automated material handling and automated part sorting system (see Fig. 1), as well as robotic bending cells and robotic welding systems for its automated processes. When evaluating new laser technology, there are two key factors that seem to resonate with most people: 1) processing more material through machines in a shorter period of time, and 2) the ability to do this within the same amount of floor space as the older equipment. For example, by taking out a lower-wattage carbon dioxide (CO2) laser and replacing it with a high-wattage fiber laser, manufacturers are able to accomplish both tasks, creating an efficiency plan that will pay off.
The next most important question is how to get higher-power laser-cut parts to the next process as fast as they can now be cut. Velocity must match velocity when looking at automation. With automated part sorting, parts are stacked as fast as the 10 kW fiber laser cuts the parts. The laser can produce up to 5X more parts per unit of time compared to a 6 kW CO2 laser, and can cut thicker parts as well. The sorting system with its dual sorting heads is able to offload the parts onto stacks that can be moved immediately to the next downstream process, and with minimal work in process storage and no backlogs attributed to manual sorting.
How are manufacturing companies achieving all of this? Randy Kinney, President of Kinney Manufacturing, notes that "98% of all parts that are processed on our laser are sorted. Common assembly parts or bending parts with similar setups can easily be sorted together to make it simple to get them to the next operation together."
Operators are able to do more with less with the right automation solution. Kinney says, "If you pair a material load-and-unload system with an individual part-picking capability, you get a combination with an unmatched benefit. One person can now load material, verify programs and cutting sequence, verify quality, and move parts to the next operation. With a shortage of skilled labor, this is a winning system. There is a climate of growth for the operator; for the company, it allows them to manage labor costs."
Kinney notes, "Automation has enabled us to pass on savings to our customers and also to reinvest for additional automated solutions. With automated loading, cutting, sorting, stacking, and robotic bending technologies, we have very flexible systems that can run in the off-shifts and with very little supervision."
Lean thinking
One might ask, what other factors move manufacturers to review these types of systems? Using the lean mindset, you need to touch the parts as few times as possible and ideally only when it involves adding value. There is no value added when manually sorting parts. After the system stacks the cut sheets, you typically need about four manual sorters moving parts and materials, and at the risk of safety issues.
With parts sorting automation, you can perform real-time parts sorting and stacking by the next downstream operation, or by like parts requiring the same press brake tooling setups or common assembly (see Fig. 2). The movement to the next operation as groups or like parts can be achieved immediately as the stacks of sorted cut parts are completed.
Programming for efficiency
The right programming and control software will further aid in the efficiency of the equipment. Programmed relief cuts in the sheets enable cut parts to be freely separated from the sheets for part sorting. Cutting plans that are quickly and easily made assist with the ability to monitor the manufacturing process. Being able to store the sorting information on a part level is key to this. Dynamic nesting is the best way to be able to nest while reducing work in process (WIP) in the shop. Once the programs are created, they are easily scheduled within the control and monitored as they are completed.
With the efficiency of sorting and moving parts to the next process, manufacturers can then find advantages in combining bending automation with standard bending. With 'like' parts already sorted together, they can make the most of optimizing press brake tooling setups.
Common parts can go to the robotic bending cells and part families to standard press brakes-thus, operators can man or monitor several machines at the same time. If a standard press brake is between two robot bending cells, a single operator can manage multiple cells during a shift. Quick changeover time on both types of bending operations keeps the process moving throughout a shift. This allows for a one-piece flow concept to reduce the need for storing for work in process.
Bending software makes this process quick and easy as it did in cutting operations. Parts are programmed offline, efficient setup sheets are created, and tools are identified for the operators. Kinney adds, "This allows us to use our existing labor to its fullest. In this lean mindset, 50- to 100-piece runs are very feasible. An average tooling setup is 3-5 minutes, with 5-6 setups per shift on robotic bending cells."
Next innovations
Kinney is always looking to the next innovations that further the ability to create a value-added process-for example, he points out that radio frequency identification (RFID) technology allows for real-time parts tracking through the shop to minimize part movement and maximize travel of parts to the next process. The RFID information is then going to be used to create heat maps for automated guided vehicles (AGVs) in the shop.
Transportation within the shop is another non-value-added expense that can be automated using AGVs. This technology allows for easy and targeted movement of parts throughout the shop, which increases material efficiency flows and saves on floor space.
Reinvesting for the future
Companies can find ways to reduce non-value-added time or processes by reviewing each step in the manufacturing process. Taking an overall view allows for the same process in a big picture. Each manufacturer can adapt the processes to create a very lean process with as few non-value-added steps as possible in the entirety. By doing so, you can get the most from each operation, using less floor space, with less labor, and less WIP. All of this will create a much faster ROI on these investments and allow for the ability to reinvest in your future.
Published in Industrial Laser Solutions, May 2021
For Kinney Manufacturing Co.