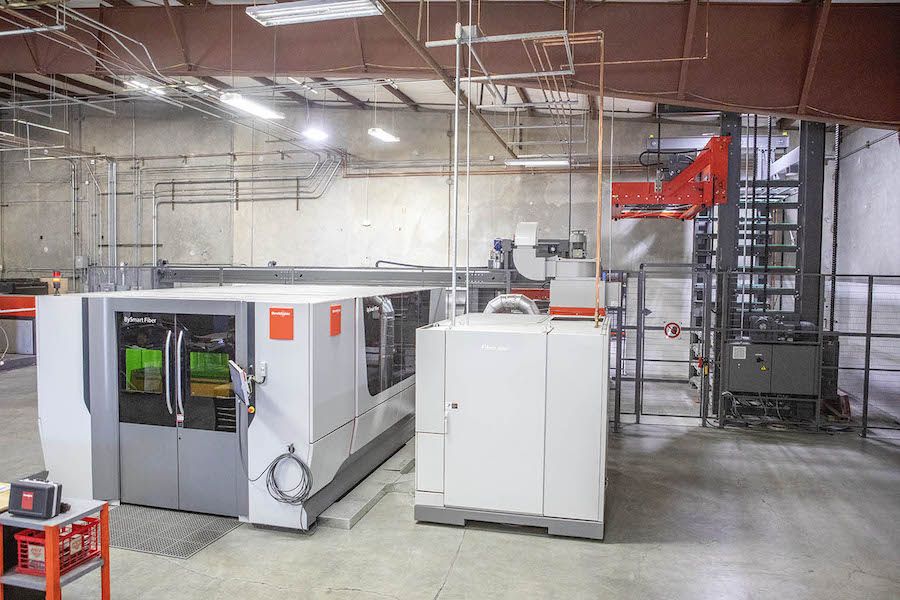
News Moving mountains
For 46 years, METALfx, a precision fabrication company, has operated out of Willits, Calif., a small town on the edge of major redwood territory. With a population of about 5,000, it's a close-knit community where everyone knows their neighbors on a first-name basis. Other than the local hospital, METALfx serves as the biggest employer in Willits with 176 employees.
When the Covid-19 pandemic first began to disrupt life in the United States, Henry Moss, president of METALfx, quickly realized that his company would be among those manufacturers considered "essential" and would, therefore, remain open. The company's customers rely on METALfx for a wide range of metal parts, including bus bars that are critical in electric power distribution and medical components that are used in a variety of end products, including medical diagnostic equipment. To continue providing these essential fabrication services, employee safety was priority No. 1.
"We're fortunate to be in a small rural town where we have great relationships within the community," Moss says. "We know the people at the hospital well, so the head of the ER department talked to us about how they were protecting their employees. Although their standards were more stringent than what ours needed to be, we developed our safety protocols based on the knowledge they shared with us."
Early on, METALfx was screening its employees, taking their temperatures and ensuring that any high-risk associates took appropriate precautions. All the while, the company was working at approximately 90 percent of pre-Covid-19 capacities - be it remotely or safely on the shop floor - to keep the critical manufacturing supply chain moving.
"Six months ago, one of our customers that makes medical diagnostic equipment never would have imagined having to triple their production," says Connie Bates, METALfx's director of business development. "But we're here for them. No matter the environment, when a customer asks for a quick lead time, we understand that theyre not trying to put us through the ringer; theyre asking because they need it. We're honored to help our customers move faster and get their products to market faster."
Wave of Benefits
In the midst of navigating his company through a pandemic, Moss was also expecting the installation of a new Bystronic fiber laser to replace the companys trio of C02 lasers. The logistics were as complicated as one might imagine, but considering the critical work being carried out at METALfx, Bystronic was committed to overcoming the challenges the pandemic had created. At the time, something as simple as air travel posed a major hurdle.
"The virus definitely threw a wrench into the normal installation cycle,says Jacob Brown, METALfx's general manager of operations. "As an operations guy, I'm always striving for efficiencies, so while we were waiting for the installation plan to be finalized, it was kind of painful to watch the C02 lasers slowly puttering away."
Fortunately, Brown didn't have to wait long. In early March, Bystronic safely and successfully brought the BySmart 6-kW fiber laser online and then returned a few weeks later to install a ByTower storage system and ByTrans Cross loading and unloading system with an extension that will allow sorting equipment to be added in the future. Even before the automation was installed, the laser cutting department went from being the biggest bottleneck on the shop floor to being a week ahead.
"l always had it in the back of my mind that the fiber laser was going to be an improvement, but it's way more impressive than I ever imagined," Brown says. "The cutting speed is phenomenal. I've never seen a look of fear like I did on the faces of our deburring guys when they saw the tidal wave of parts coming off of the new laser. The challenge will be dealing with the capacity gains that it delivers, but we are prepared for that and are bringing in new equipment to support them."
In addition to the sheer speed of the BySmart, METALfx made the switch from C02 to fiber based on a handful of advantages and features. Benefits such as shorter setup times, lower operating costs and reduced maintenance played into the ultimate decision, but the need to handle a wider range of material types and thicknesses also served as a deciding factor.
"The fiber laser is a disruptor," Bates says. "A C02 laser can be a fabulous piece of equipment, but the fiber has advantages that we simply couldn't have replicated in-house. We live in a world that's all about working smarter, faster and better, and really, that was the main point for us when we moved from C02 to fiber: What worked for manufacturing even two or three years ago isn't good enough today."
Ample Automation
As a standalone piece of equipment, the BySmart fiber laser delivers a slew of benefits - especially in the speed in which it processes a sheet of metal. Overall, it cuts material five times faster than a C02 laser. Speeds for cutting steel and stainless steel less than 5/16 in. thick can be even faster, but therein lies the issue.
"From day one, I've said that I'm not going to invest in fiber until I have the money to invest in automation, as well," Moss explains. "It would have been beneficial to get a new laser a year ago, but we knew we needed the full package with the automation."
Moss decided the only way the team at METALfx could keep up with the BySmart would be with the help of the ByTower storage system and ByTrans Cross loading and unloading system. Without those additions, parts coming off of the laser would pile up as downstream operators struggled to keep pace. But for Moss and the rest of the team, the additional investments weren't just about avoiding bottlenecks. He envisions his company moving into lights-out manufacturing, running orders on holidays or overnight, improving the utilization of the key employees that program jobs, and improving overall efficiency and margins.
"The most important thing for us to understand and embrace is the paradigm shift that the new laser represents," Bates says. "From my perspective, it's like Superman came flying into our facility. IVs exciting, but we have to have a plan for how to harness all of that potential. If the investment was made just because it cuts things faster, then we won't be able to harness all of its capabilities. We have to change the way we think and allow ourselves to be motivated to move forward into the future with it."
Part of that goal is accomplished with the automation, but part of it is also realized through Bystronic's ByCockpit and BySoft software. The data that can be gathered from a laser can be quite powerful when a company chooses to use it.
"The ByCockpit software is coupled with a camera inside of the machine that allows us to monitor the cutting process in real time," Moss says. "It also features dial indicators that give us the ability to produce daily, weekly and monthly performance reports. Being able to monitor and track the laser in such a focused way will give us new insights for how we're moving parts off of the laser and to the next area. It's still new to us, but we're anticipating significant changes."
Fully harnessing the power that's baked into the BySmart's software, however, requires experience or extensive training. Fortunately, METALfx has a handful of employees that had worked with Bystronic software in the past.
"We're pretty blessed with the longevity of some of our associates here," Brown says. "Some of the things theyve done in the past on the C02 translate over to fiber, but not everything, so we've had to break old habits that are no longer valid or necessary. Overall, the process to make a good part is very similar, so they're applying years and years of experience to maintain our quality standards. The nesting capabilities alone have been outstanding and have increased our productivity multiple times over."
There is always a bit of trepidation on the shop floor when a new piece of equipment is brought in - no one said that change is easy. But, when company leadership is communicative and transparent, change is definitely easier to embrace.
"The investment in the laser and the automation shows our commitment to move into new technology," Brown says. "We've always been growth minded, and the laser is a daily reminder of that. To continue to be successful, we have to advance the technologies on our shop room floor. To say the least, the laser has become a statement piece of that very idea."
The Big Picture
METALfx had been planning and preparing for the eventual switch to fiber laser technology for some time. And now that the BySmart is on-site, the company can put all of its focus on future growth instead of dealing with bottlenecks or otherwise outdated equipment. As Moss told his staff early on, there is no playbook for how to navigate a company through a pandemic. Having a robust infrastructure, however, can ease minds and instill confidence, even in the face of uncertainty.
"Typically, you'd be hesitant to say that anything good can come from something like a pandemic, but it's made the team stronger and closer than ever before, and that includes our customers," Moss says. "We have customers that are struggling, so we feel fortunate that we can work with them to get through this - whether it's holding inventory for them or working on payment terms."
METALfx has always focused on developing long-term relationships, which has created an incredibly diverse customer base for the company. Customers fall in the Fortune 500 category, but METALfx also has customers with 40 employees and fewer. Regardless of size, Moss considers all of the companys customers as essential. They serve a variety of industries, including food processing, medical, transportation, communications, test and measurement, and semiconductor. Ultimately, the agility the new fiber laser and ancillary automation brings to the table will fortify those relationships even more.
"The laser has already been a transformative piece of equipment for us," Moss concludes. "It's not like replacing an old spot welder with a new spot welder; it's about everything that feeds into the entire cutting process just as much as it's about post-processing. In the business of sheet metal fabrication, it's almost something that you can't afford not to have. And now that we have it, it's full steam ahead."
Shopfloor Lasers - June 2020For METALfx of Willits, CA