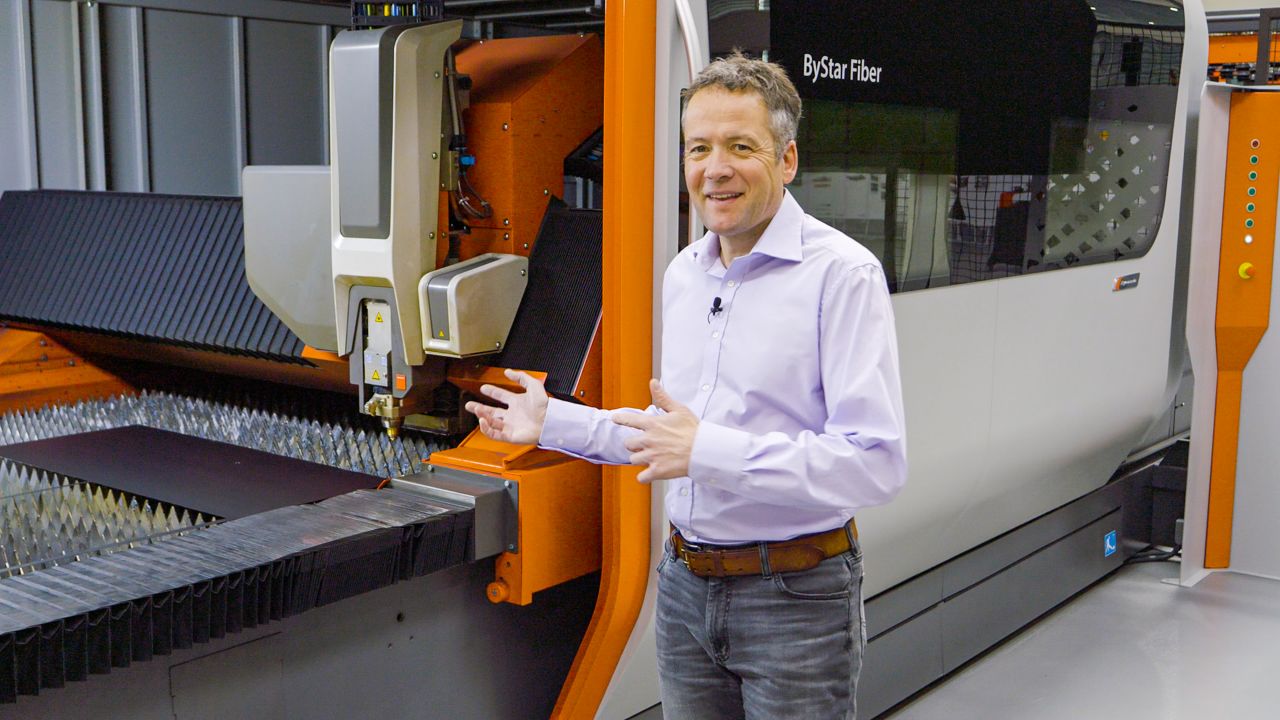
Machine downtime How to reduce downtime by up to 30%
The causes of machine downtime are manifold. On the one hand, there are technical error sources such as defective components, mechanical causes, or software malfunctions. On the other hand, operational triggers can lead to machine downtime, for example, programming errors or incorrectly handled parts.
Generally, good maintenance reduces downtime by up to 30 percent. Our customized service packages also keep the risk of technical errors low. And to counteract operational errors, we offer you various training options. If your machine should come to a standstill after all, our support and our 820 service technicians at 40 locations worldwide ensure that your system is up and running again quickly.
Avoid machine downtime Minimize downtime and maximize uptime
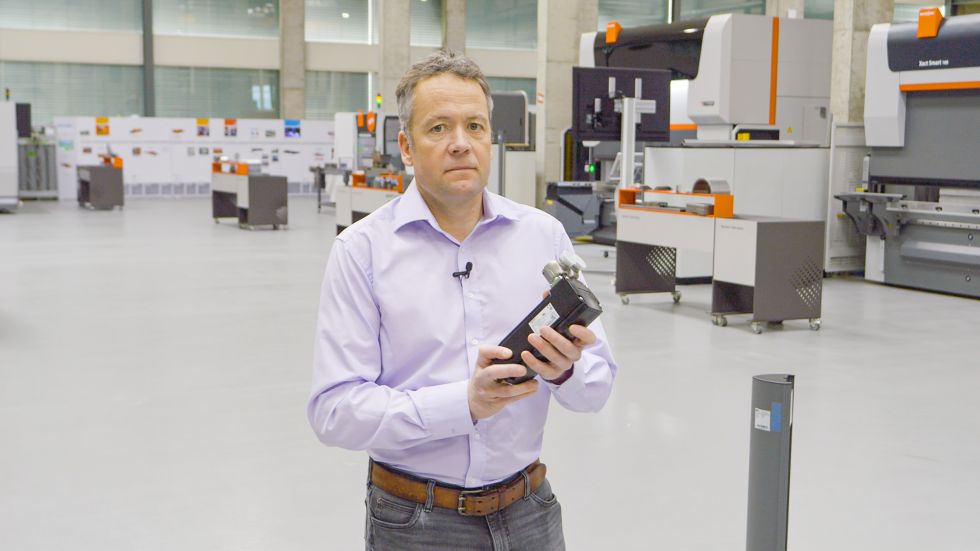
In the field, our service teams often encounter a number of error causes that can be avoided with little effort. With the following tips, you can reduce your downtime to a minimum.
Tip 1: Clean your machines regularly
Contamination can lead to machine downtime. Therefore, take the cleaning of your systems just as seriously as the production of your parts. This way, you can proactively prevent downtime. To ensure that cleaning is not neglected, you should integrate this important task into your production processes, for example with checklists.
Tip 2: Keep important spare parts in stock
Important spare parts must be kept in stock on site. This massively shortens downtimes. It is annoying when machine downtime stops production just because you have to wait for a spare part to arrive. Of course, our web store is open around the clock, but you should still keep essential parts on hand at all times. We also recommend that you use original spare parts. This will pay off in the long run because they are more durable and replicas can damage the machine.
Tip 3: Use latest generation technologies
Use the latest Bystronic technology. This ensures smooth operation. In many cases, a retrofit is possible because the parts are compatible. For example, if your laser cutting machine is 5 to 6 years old, it is worthwhile to use the latest generation of cutting heads. In this way, you benefit from the immense progress made in recent years.
Tip 4: Train your employees
Well-trained employees are essential for restarting production quickly in case of a shutdown. But that is not all: around half of the machine downtime is due to incorrect handling. Therefore, it pays off to invest twice in employee training. Equipped with the right know-how, well-trained employees can reduce your downtime to a minimum. At the same time, fewer operational errors occur, which maximizes uptime.
Avoid machine downtime Minimize downtime and maximize uptime
In the field, our service teams often encounter a number of error causes that can be avoided with little effort. With the following tips, you can reduce your downtime to a minimum.
Tip 1: Clean your machines regularly
Contamination can lead to machine downtime. Therefore, take the cleaning of your systems just as seriously as the production of your parts. This way, you can proactively prevent downtime. To ensure that cleaning is not neglected, you should integrate this important task into your production processes, for example with checklists.
Tip 2: Keep important spare parts in stock
Important spare parts must be kept in stock on site. This massively shortens downtimes. It is annoying when machine downtime stops production just because you have to wait for a spare part to arrive. Of course, our web store is open around the clock, but you should still keep essential parts on hand at all times. We also recommend that you use original spare parts. This will pay off in the long run because they are more durable and replicas can damage the machine.
Tip 3: Use latest generation technologies
Use the latest Bystronic technology. This ensures smooth operation. In many cases, a retrofit is possible because the parts are compatible. For example, if your laser cutting machine is 5 to 6 years old, it is worthwhile to use the latest generation of cutting heads. In this way, you benefit from the immense progress made in recent years.
Tip 4: Train your employees
Well-trained employees are essential for restarting production quickly in case of a shutdown. But that is not all: around half of the machine downtime is due to incorrect handling. Therefore, it pays off to invest twice in employee training. Equipped with the right know-how, well-trained employees can reduce your downtime to a minimum. At the same time, fewer operational errors occur, which maximizes uptime.
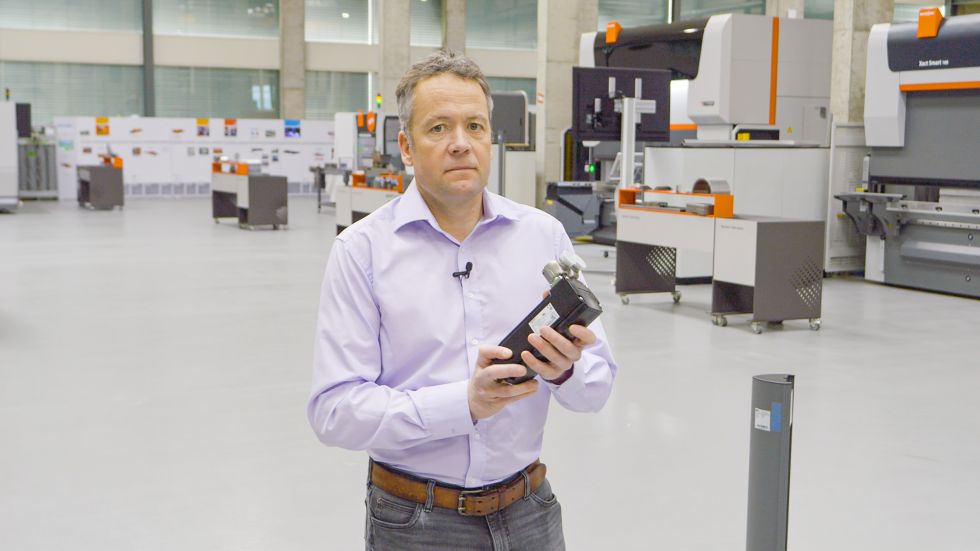
Want to know how to reduce machine downtime by up to 30%?
"Operating errors cause around half of machine downtimes"
Michael Jost, Global Head of Enablement & Governance Service, explains how machine downtime can be prevented.
Speed is crucial in the event of machine downtime. How does Bystronic ensure rapid assistance?
To ensure that our customers receive support quickly and without complications, our support is built on several pillars: hotline support, remote support, and self-help. In addition, local service technicians are available worldwide to provide rapid on-site assistance. Currently, there are around 820 service professionals at 40 locations. And we are constantly expanding our service teams.
Is service on-site usually mandatory?
No, not at all. In many cases, malfunctions can be remedied in other ways. But that presupposes that we have well-trained contacts on the customer side. Trained employees can not only identify problems but also solve them independently.
How can customers get specific training?
Bystronic offers certified training courses. These are based on a combination of theoretical and practical training sessions. In this way, our customers learn how to solve problems themselves. If we pull together, machine downtime will be massively reduced.
What are the main causes of machine downtime?
It varies depending on the setup. If a single machine goes on strike, the cause is usually quickly found. In laser cutting, for example, parts in the cutting process and around the cutting head are a source of defects. As a rule, such defects can be rectified quickly.
In which cases is error analysis more tricky?
Today, production is increasingly automated. This has not only massively increased the speed, but also the complexity of the systems. This makes fault analysis more demanding. In addition to mechanical faults, electronic faults also occur or those that are software or interface based.
Are you looking for a customized service? We are here for you!
What other reasons can lead to machine downtime?
Around half of the downtime is caused by operational errors. These can be, for example, part collisions due to incorrect operation or programming errors.
How can sheet metal workers prevent such errors?
The best prevention is intensive operator training. This pays off in two ways: If in-house know-how is available, errors are found and rectified more quickly. In addition, professional handling reduces the error rate. We offer various training courses and programs for this purpose.
And what is Bystronic doing to reduce machine downtime?
We invest a lot in the training of our employees. With their comprehensive expertise, they have our customers' backs. On the other hand, we use new technologies to support our service teams.
For example?
The keyword is connectivity. Through proactive and predictive maintenance, we can significantly reduce downtime. And our hotline staff have even better insight into our customers' production thanks to real-time data.
Are there other innovations to prevent machine downtime?
Yes. For example, it happens that sheet metal workers run out of nitrogen. With our N2 generator, this no longer happens. This saves money and makes us independent of suppliers and price increases. It also reduces the CO2 footprint. As a rule, this acquisition is amortized after a short time.
In summary: How can you maximize uptime?
For production to run smoothly, cooperation is necessary. If sheet metal workers clean their machines carefully, they already reduce the risk of machine downtime considerably. Regular maintenance is just as important. A well-maintained machine can reduce machine downtime by up to 30 percent. Our modular service packages allow maintenance work to be optimally tailored to your own needs.
«A well-maintained machine can reduce machine downtime by up to 30 percent.»
Michael Jost, Global Head of Enablement & Governance Service
Proactive support in the event of machine downtime
From our 360° Customer Advisor
To prevent downtime, receive expert advice from our 360° Customer Advisor during a Bystronic service. This involves analyzing strengths and weaknesses in your production:
- Inspection of critical components to increase productivity
- Comprehensive inspection of workflows, systems and accessories
- Verification that the machine is properly maintained
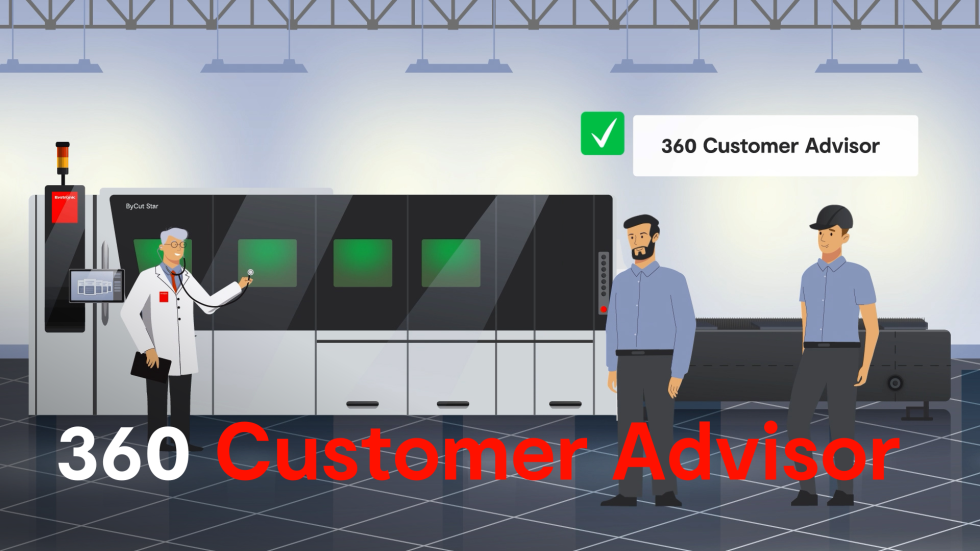
Bystronic Care Packages
Tailor-made service for you