A legacy of firetrucks
Every vehicle is custom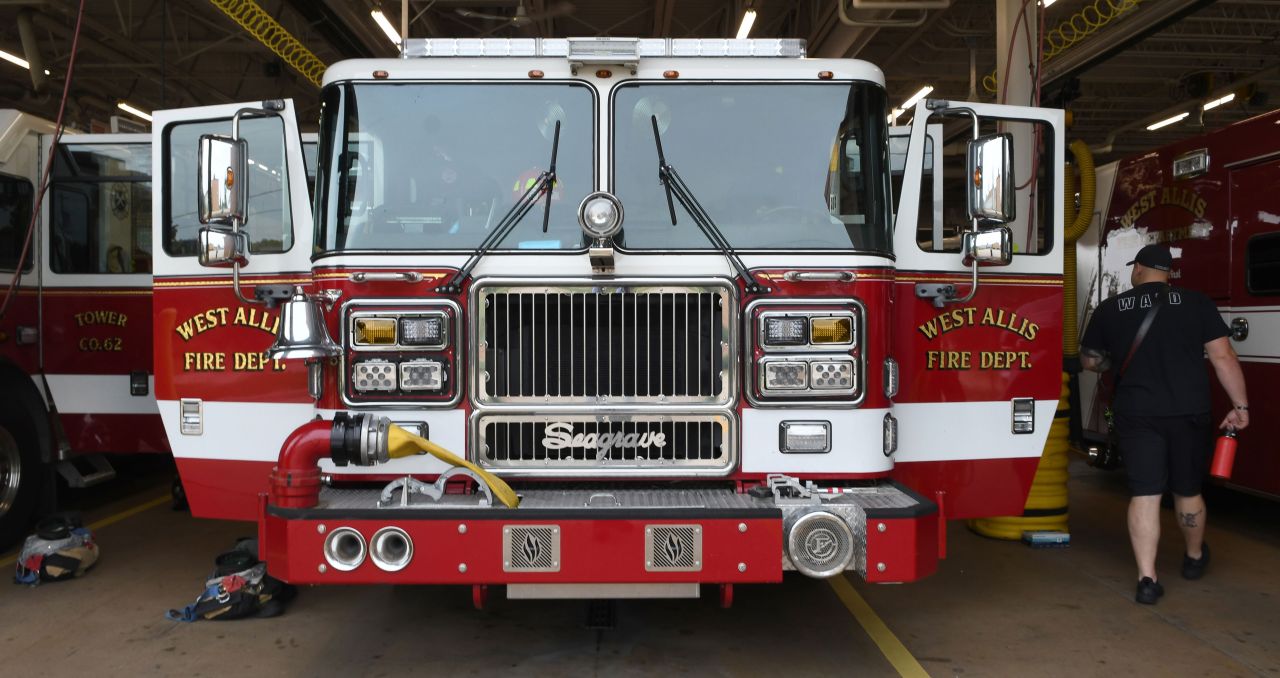
Every fire truck from FWD Seagrave is unique. Accordingly, the batch sizes in sheet metal processing are small. With Bystronic systems, the US manufacturer has the necessary flexibility to fulfill all the special requests of the fire departments.
FWD Seagrave is one of the pioneers in the manufacture of fire trucks. The company has a history spanning over 140 years. Daryl George has witnessed almost 30 of those years. During this time, a lot has changed. "When I started here, you could only place a single sheet of metal in the machines," recalls the operations manager.
Today, productivity is significantly higher – thanks to modern fiber lasers and the ByTrans 4020 Extended automation solution:
"We set up the Bystronic systems once, and they work through ten inches of sheet metal, with sheets of varying thicknesses made from different materials: aluminum, steel, or stainless steel."
High variety of variants
The high flexibility in terms of materials and sheet thicknesses is crucial for FWD Seagrave. Each vehicle is tailored to the individual wishes of the customers. In the narrow streets of New York, for example, it is not possible to extend four stabilizing legs during firefighting operations. Therefore, the in-house engineers have to find a solution for just two supporting legs.
Accordingly, the variety of installed parts is large. The laser cutting systems and press brakes from Bystronic ensure that many of the over 500,000 construction and spare parts in the warehouse can be quickly reproduced. About half of these are manufactured by the company itself – a rarity for a vehicle manufacturer. Most of FWD Seagrave's competitors produce significantly less in-house.
Quick retooling thanks to smart features
The average batch size in sheet metal processing is just four pieces, according to Daryl George. This means constant retooling of the machines. The intelligent functions of the systems, such as the Laser Angle Measuring System (LAMS), support this:
"The angle measuring system of our bending machine ensures short retooling times," notes the operations manager.
Around 20,000 parts are installed in the trucks, which can weigh up to 35 tons. This takes time: it usually takes eight to 14 months from order to delivery – currently longer due to the good order situation. Each year, a little over 100 vehicles are produced at the Clintonville, Wisconsin, manufacturing facility.
Quality over price
The prices for the large trucks range between $600,000 and $1.7 million. This places the manufacturer in the upper price segment. After the financial crisis of 2008, there was a phase when some customers switched to cheaper manufacturers, recalls Daryl George. However, the higher maintenance costs made many reconsider. Those who look at the total lifecycle costs ultimately find that FWD Seagrave's high-quality vehicles are more cost-effective.
FWD Seagrave also places high demands on its suppliers:
"All our forklifts are from Toyota, the welding machines are from Miller, and the equipment for property maintenance is from John Deere. Bystronic is also one of the partner companies with which we have built a close relationship over the years," says Daryl George.
His team has been cutting and bending on the provider's systems for over 20 years. This is unlikely to change anytime soon.