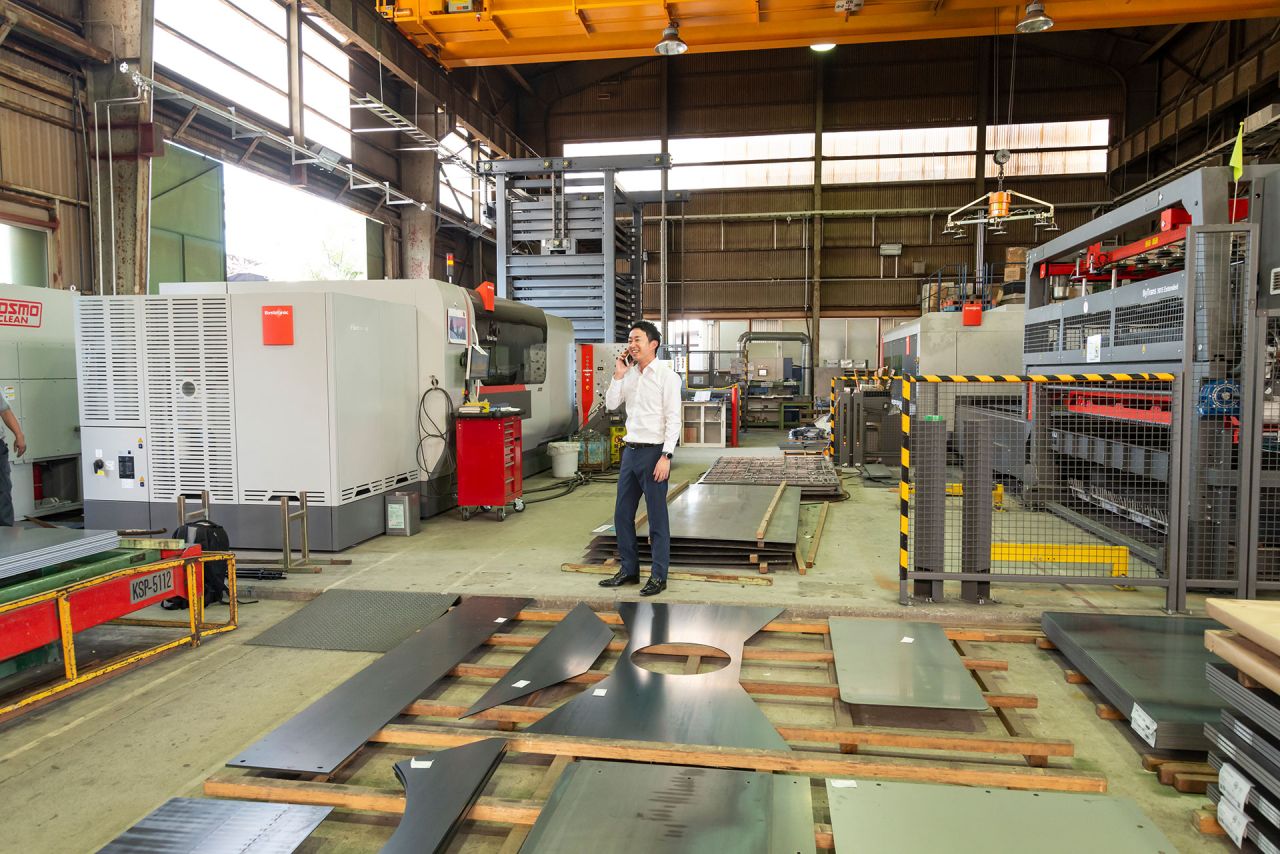
News Brennpunkt Nagoya: Ein Traditionsbetrieb im Herzen der Autoindustrie
Tokio, Hauptbahnhof. Wie ein Pfeil vor dem Abschuss steht sie da, die rollende Legende: der Shinkansen. In ihm, dem schnellsten Zug der Welt, spiegelt sich vieles, was Japan zu dem gemacht hat, was es heute ist: eine Hightech-Nation, die zu besuchen einer Reise in die Zukunft gleichkommt. Wo man hinschaut, findet man modernste Technologien und innovatives Design. So auch im Shinkansen. Ein Beispiel dafür sind die drehbaren Sitze, die sich bei Bedarf auch gegen die Fahrtrichtung drehen lassen.
Mit geschlossenen Augen unterwegs nach Nagoya nimmt man die enorme Geschwindigkeit, über 320 Stundenkilometer in der Spitze, kaum wahr. Nur wenn man aus dem Fenster blickt, wird sie einem bewusst. Neben der technischen Perfektion zeigt sich im Shinkansen auch die ausgeprägte Dienstleistungsmentalität der Japaner: Wer Hunger oder Durst hat, muss nicht lange warten, bis das überfreundliche Servicepersonal vorbeikommt und Snacks anbietet.
Im Brennpunkt der Autoindustrie
Im Nu erreicht man das 366 Kilometer entfernte Nagoya. Eindreiviertel Stunden dauert die Fahrt in die 2,5-Millionen-Stadt, die als Brennpunkt der japanischen Autoindustrie gilt. Hier produzieren sie alle: Toyota, Honda, Nissan, Mitsubishi und Mazda. Nagoya erwirtschaftet ungefähr das gleiche Bruttoinlandsprodukt (BIP) wie ganz Norwegen. Der Frachthafen und die gut ausgebauten Transportwege spielen einer reibungslosen Logistik in die Hand; rund um die bekannten Autohersteller haben sich über die Jahre viele Zulieferer angesiedelt. Eine Firma, die hier produziert, ist das Familienunternehmen Daisan Kouki. Es ist seit 70 Jahren fest in Familienhand: «In den 60er-Jahren war Daisan Kouki ein reiner Familienbetrieb», erzählt Noriyuki Wakahara. Er leitet das Unternehmen mit 120 Mitarbeitenden in der dritten Generation. Das Kerngeschäft des Firmengründers, seines Schwiegergrossvaters, sei der Handel mit Blechen gewesen. «Als ein Kunde eines Tages fragte, wieso man eigentlich nicht auch Bleche verarbeite, ging uns ein Licht auf», erinnert sich Noriyuki Wakahara.
Im Jahr 2004 machte Daisan Kouki Nägel mit Köpfen, kaufte einen 2-Kilowatt-Laser und begann, Bleche zu bearbeiten. In den Folgejahren wurde laufend erweitert – auch weil die Sicherheitsanforderungen für den Erdbebenschutz Jahr für Jahr gestiegen sind. «Weil wir alle Anforderungen an Qualität jederzeit verlässlich erfüllen konnten, haben wir uns in der Branche einen guten Namen gemacht. Ein Grossteil der Kunden ist in der Automobilbranche angesiedelt. Die Teile, welche Daisan Kouki herstellt, unterstützen die Produktion vor allem in der Herstellung der Produktionskette.
Lesen Sie die ganze Geschichte in der digitalen Version des World Magazins.