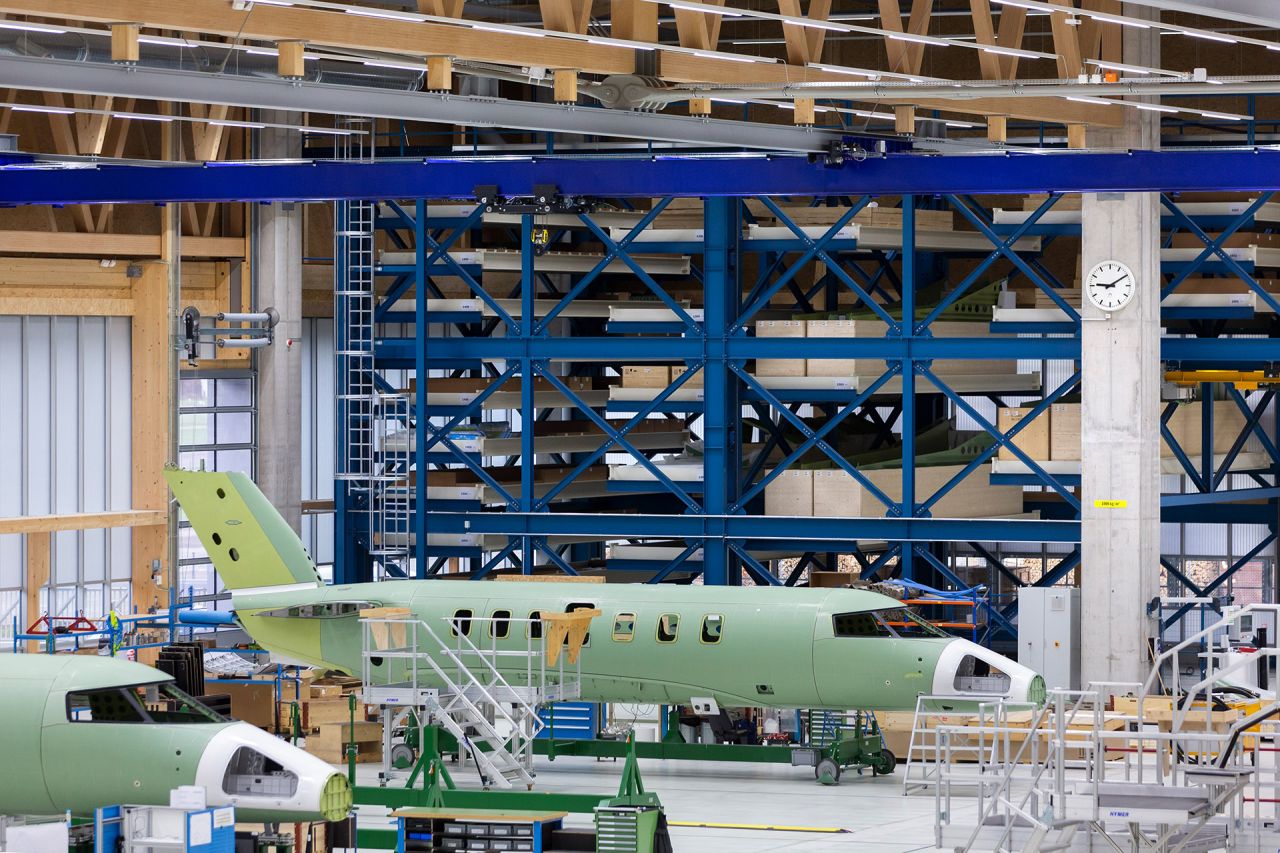
News A puzzle with more than 10,000 pieces
Today is certainly not perfect flying weather. This is a stormy day. Trying to spot planes in the sky above the airfield in Buochs would be futile. Not so, however, in the Structure Assembly Hall S, the 200-meter long newly erected building right next to the runway. Here they are lined up in a row: Aircraft fuselages in various phases of completion. They are the latest model in the fleet of Aircraft Ltd, the PC-24. On average, one of these ultra-versatile jets leaves the factory in central Switzerland every week. For almost a year now, the Bystronic subsidiary FMG has been making an important contribution towards ensuring that this process runs smoothly. With a customized overhead warehouse.
Because aircraft engineering is not just a technical challenge but also a logistical one: At the Pilatus competence centre for structure assembly operations, more than 10,000 individual parts – from the 7-meter side panel to the individual rivets – are installed to form the PC-24. In order to ensure uninterrupted production, each part must be in the right place at the right time. It is Thomas Gosso’s job to guarantee this. The Logistics Team Leader oversees three different storage systems: “We have a small-parts warehouse, a shuttle for medium-sized assemblies – and the FMG overhead warehouse for parts that require a par - ticularly large storage space.”
An efficient and flexible custom design
Twice a day, a truck pulls up to the goods receiving area and delivers parts that were manufactured just a few hundred meters away at the factory in Stans; approximately twice a week, components from external suppliers also arrive here. Like just now: The Pilatus logistics experts remove the screws from the wooden shipping crate. Under the lid, wing panels for the PC-24 are exposed – in “primer green”, the matte green color of all aircraft parts before they are painted. The employees give commands to the storage and retrieval system via the central warehouse management system. Using the integrated over - head crane, they hoist the parts into the 10-meter long and 2-meter wide steel cassettes of the overhead warehouse. There are 62 cassettes in the warehouse, with four different loading heights between 60 and 250 centimeters.
Although each cassette has a fixed bay in the overhead warehouse, it is also equipped with a buffer zone where cassettes can be temporarily deposited. This enables Pilatus to respond flexibly to deliveries and orders and to load and unload efficiently. Sensors ensure the safety of the employees, guaranteeing that the cassettes are loaded correctly, and that no components project beyond the side walls or the maximum loading height. This prevents damage that could result in high costs.
The functions have proven themselves to be effective – especially considering that the overhead warehouse is not a standard solution, but was designed specifically for the production processes in the new structure assembly hall. This presented very specific challenges, as Thomas Gosso recalls: “All the values in the functional specifications for the warehouse solutions were based on assumptions – the building did not even exist yet. Which is all the more reason why I am satisfied that everything is now running so smoothly.” There were a few initial teething problems, but thanks to Bystronic’s expert service, every mal - function was quickly resolved.