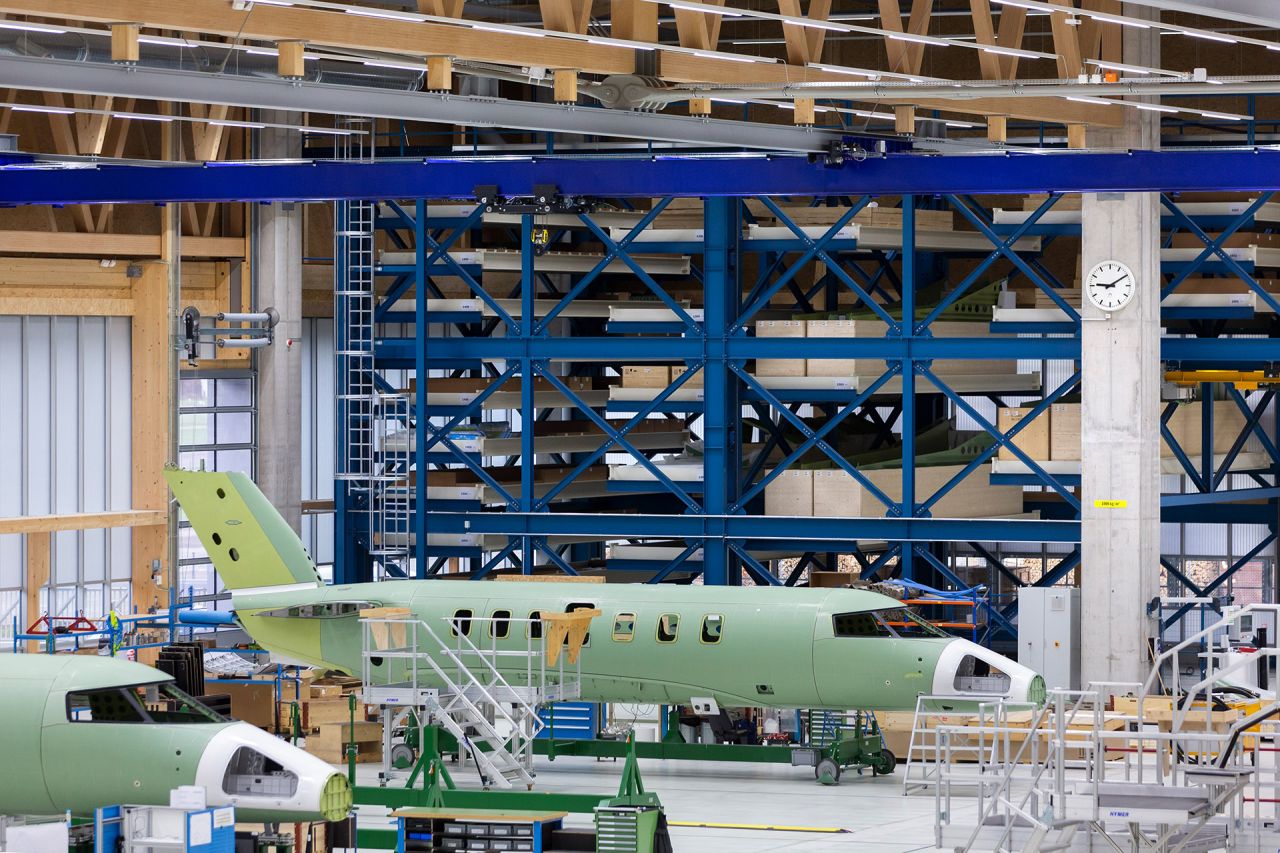
News Un puzzle di oltre 10.000 pezzi
Nonostante l’impegno massimo, oggi le condizioni di volo non sono proprio perfette. Giornata di tempesta. Dalla pista di atterraggio di Buoch si scruta il cielo alla ricerca di velivoli, invano. Ma non nel capannone S, la nuova costruzione lunga 200 metri, situata a bordo pista, dove gli aerei sostano in fila ordinata. Le fusoliere in diversi stadi della produzione. Si tratta del PC-24, il nuovissimo modello della flotta di Pilatus Flugzeugwerke AG. Mediamente ogni settimana uno di questi Super Versatile Jet lascia gli stabilimenti produttivi della Svizzera centrale. Da quasi un anno anche l’affiliata FMG di Bystronic dà un importante contributo affinché il processo produttivo si svolga senza alcun problema, grazie all’utilizzo di un magazzino carrabile personalizzato.
Di fatto la costruzione di un aereo è un capolavoro non solo tecnico, ma anche logistico, nel quale oltre 10.000 diversi pezzi, dalla parete laterale lunga 7 metri fino ai singoli rivetti, vanno a comporre la struttura di un PC-24. Per garantire una produzione senza problemi, ogni pezzo deve trovarsi al posto giusto nel momento giusto. E questo compito spetta a Thomas Gosso, il team leader della logistica, che controlla tre diversi sistemi di immagazzinamento: «Abbiamo un magazzino per la minuteria, uno shuttle per componenti di media grandezza e il magazzino carrabile FMG per i pezzi più voluminosi.»
Una produzione fuori serie efficiente e flessibile
Due volte al giorno un camion arriva all’ingresso merci e consegna pezzi prodotti a poche centinaia di metri di distanza, negli stabilimenti di Stans; più o meno due volte la settimana arrivano anche i componenti di fornitori esterni, proprio come sta accadendo ora: Gli addetti alla logistica di Pilatus rimuovono le viti dalle casse di legno. Da sotto il coperchio sbucano i rivestimenti per le ali del PC-24, nel loro «primer green», il colore verde opaco che hanno tutti i componenti per aereo prima della verniciatura. Attraverso il sistema di gestione centralizzata del magazzino gli operai guidano il trasloelevatore. Col carroponte integrato sollevano i pezzi nelle cassette di acciaio lunghe 10 metri e larghe 2, del magazzino carrabile. Sono 62 le cassette nel magazzino, disposte in quattro diverse altezze di carico tra i 60 e i 250 cm.
Sebbene ogni cassetta abbia un posto fisso nel magazzino carrabile, esso è dotato anche di una «zona cuscinetto» in cui è possibile riporre temporaneamente le cassette; ciò consente di reagire in maniera flessibile alle consegne e agli ordini e di ottenere un carico e scarico efficiente. I sensori garantiscono il rispetto della sicurezza dei lavoratori e fanno in modo che le cassette vengano caricate correttamente e che i componenti non sporgano dalle pareti laterali o dall’altezza di carico. In questo modo è possibile evitare costosi danni.
Le funzioni sono sorprendenti, soprattutto considerando che il magazzino carrabile non rappresenta una soluzione standard, bensì una costruzione ideata appositamente per la produzione nel nuovo capannone. Una soluzione carica di sfide, come ricorda Thomas Gosso: «Tutti i valori contenuti nelle specifiche tecniche per le soluzioni di magazzino si basavano su ipotesi perché il capannone non esisteva ancora. E adesso sono ancora più soddisfatto pensando che tutto funziona al meglio.» Certo, all’inizio il sistema ha incontrato alcuni problemi, ma poi, grazie all’assistenza competente, è stato possibile superare velocemente ogni disguido.