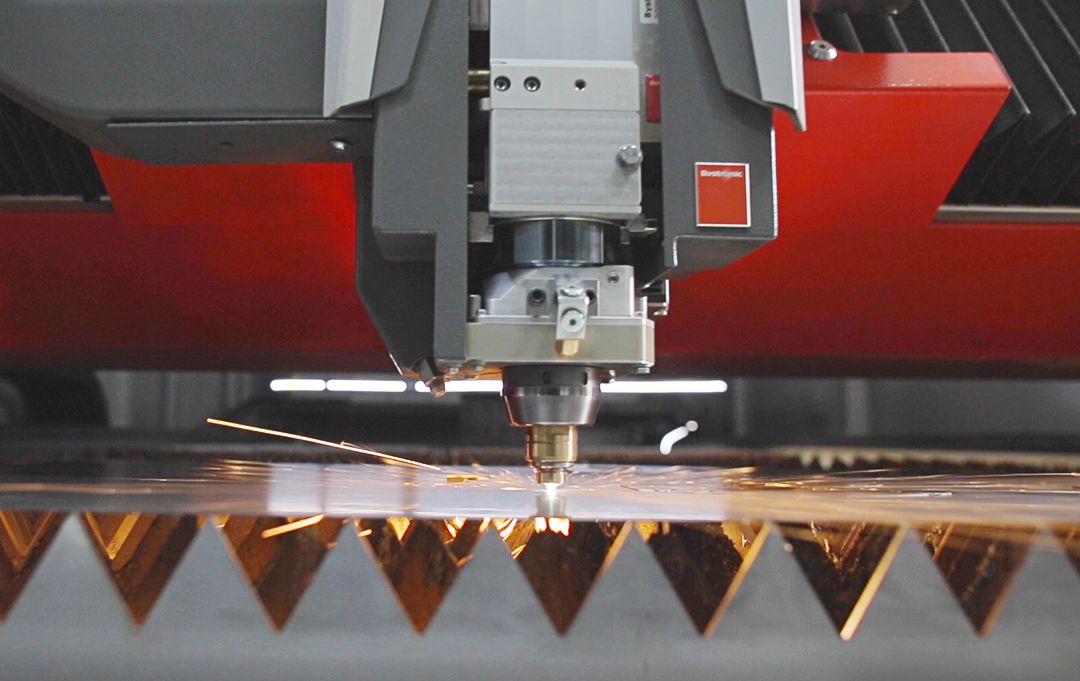
News Profiting With High-Power Fiber Lasers
Advancements in high-power Fiber laser cutting technology continue at an incredible pace and the benefits are quickly being realized by fabricators. Power levels up to 20kW are quickly being adopted for sheet metal cutting and the speed and throughput of these laser cutting systems are setting new standards in productivity and efficiency.
Since converting from C02 to Fiber, many fabricators have acknowledged the higher throughput increase when utilizing fiber lasers, regardless of the kW power range. Many fabricators have already made adjustments to their processes to accommodate the higher throughput, both with front-end programming systems and with material handling automation. The move to double-digit Fiber laser power creates additional considerations with respect to maintaining throughput demands and lowering operating costs.
With throughputs of up to three times more parts per unit of time compared to single-digit kW fiber lasers, additional considerations need to be taken into account to maintain a high machine utilization rate and lower operating costs when utilizing high-speed fiber laser powers above 10kW.
Automating the Front-End Process
By utilizing an Order Management System, companies are able to streamline the entire process by interfacing with their existing ERP (Enterprise Resource Planning) system. This enables them to process their parts automatically, from incoming orders to finished cut parts. An effective Order Management System can take incoming orders and search for the correct DXF part files and automatically program parts based on their material characteristics, then nest and schedule to the appropriate machine. Scheduling can be defined by the due date or job priority. The triggering of a job can be delayed until the clearly defined latest possible point in time, while still guaranteeing forecasted delivery deadlines.
An Order Management System maximizes the selection of parts and efficiently distributes all the orders that have been released by the ERP system to the various cutting plans. Cutting plans can be automatically released to the machines based on achieving the required material yields. This leads to more parts per sheet, better material utilization, and better delivery forecasts.
Automated Sheet Nesting
In addition to creating timely nests, programming systems must also consider sheet material utilization as this is a key element in the overall cost per part. With material making up 50% to 75% of the total cost per part, a programming system must take into consideration the ability to optimize material utilization. Also important is the time it takes to process the nest, which is a function of the laser processing speeds and the cut path optimization.
Reducing the time from the order to the cut part, reducing material utilization costs, and reducing processing times are all key elements to maintaining competitiveness and profitability.
Advancements with Cutting Gases
In addition to Fiber laser power advancements, there have also been significant advancements in the development of cutting parameters utilizing different gases and mixing techniques. While oxygen and nitrogen assist are the mainstay for most laser cutting applications, significant cost reductions, and performance benefits have been realized utilizing either a dedicated or engineered Nitrogen generation system for cutting with nitrogen, and as well, introducing a certain percentage of oxygen into the nitrogen cutting process (mixing) for increased speeds and edge quality. While investments in nitrogen generation equipment can be high, the value of generating your own high purity nitrogen on-demand, coupled with the significant reduction in nitrogen gas costs and elimination of costly rentals, delivery, and long term contracts is very appealing and can pay for the initial investment in a relatively short time frame.
Automating Part Sorting
The unloading process is extremely critical as all other processes of loading and cutting are dependently tied to this very important sequence. A bottleneck is created without the unloading taking place in a timely manner. At this point, there are two ways to address the unload automation process. One method is to unload the entire cut sheet with parts using an unload fork system. Another, and more efficient method, is to already have the parts unloaded using an automated sorting system for the parts and a fork system to remove the material skeleton when completed. The automated sorting system sorts parts from the sheet based on the order it belongs to. It also organizes ‘like’ parts in a neat stack for the next process. This greatly reduces process times in sorting the parts manually from the cut sheet and reduces errors in stacking similar part revisions. Parts can move directly to the next process as they are finished cutting.
Fiber Lasers’ Impact
There is no denying the impact that Fiber lasers have made on the metal fabrication industry. Fiber lasers have increased speed and throughput, reduced costs due to their higher electrical efficiencies, and eliminated much of the maintenance costs associated with legacy CO2 systems.
As a result of the higher throughput, companies have had to upgrade their supporting systems; programming systems, automated material handling, and part sorting systems as well as gas delivery systems. Fiber lasers have forced metal fabricators to improve their processes in support of the throughput capabilities of their Fiber laser cutting equipment. Continued improvements in fabrication processes and lower costs per part will continue to develop as higher Fiber laser powers are utilized. Companies that adopt these technology improvements will carve out a unique position in their marketplace and see significant revenue as a result.
By Frank Arteaga, Regional Director of Marketing, Bystronic Inc., Hoffman Estates, IL